Конструктивные элементы судовых систем
ТРУБЫ
Они характеризуются материалом, из которого изготовляются, диаметром и толщиной стенки. В системах судов внутреннего плавания применяют главным образом трубы из углеродистой стали: бесшовные,, электросварные и водогазопроводные (газовые). Последние поставляют с резьбой на обоих концах или без нее. Водяные трубопроводы изготавливают из стальных оцинкованных труб; они обладают большей коррозионной стойкостью, чем неоцинкованные.
В системах судов на подводных крыльях для уменьшения массы используют трубы из алюминиевых сплавов. Такие трубы получили распространение на катерах и судах с корпусами из легких сплавов.
Для фреоновых трубопроводов диаметром до 20 мм в системах охлаждения применяют медные трубы. Иногда их используют в трубопроводах горячей воды и фекальной.
Применяют в судовых системах также стальные трубы, футерованные изнутри полиэтиленом, и полиэтиленовые. Для морской воды часто используют медные трубы. В установках, по трубопроводам которых движется озоно-воздушная (озоно-водяная) смесь, применяют трубы из легированной стали.
В системах сжатого воздуха высокого давления обычно используют биметаллические трубы, имеющие снаружи стальной слой, а внутри-плакировочный красно-медный. Находят применение в некоторых системах (например, фановой) стальные бакелитированные трубы.
Размеры труб, изготовляемых отечественными заводами, марки материалов и требования к трубам определяются соответствующими государственными стандартами.
Получили распространение в судовых системах трубы как круглого, так и прямоугольного сечения. Последние целесообразны для систем вентиляции и кондиционирования, имеющих трубопроводы большого сечения.
В государственных стандартах на сортамент труб регламентированы их размеры по наружному диаметру и толщине стенки. Для каждого наружного диаметра трубы предусмотрено несколько толщин стенки. Так, например, стальная сварная труба наружным диаметром 102 мм (ГОСТ 10704—76) может выполняться с толщиной стенки: 2,0; 2,2; 2,5; 2,8; 3,0; 3,2; 3,5; 3,8; 4,0; 4,5; 5,0; 5, 5 мм. Таким образом, при постоянном наружном диаметре трубы внутренний диаметр ее может быть различного значения.
Для сокращения числа типоразмеров труб, используемых при постройке судов, в судостроении введены нормали, ограничивающие государственные стандарты. Это позволяет существенно снизить стоимость постройки и ремонта судовых систем. Кроме стандартов, регламентирующих размеры труб и технические требования к последним, имеются государственные стандарты, устанавливающие условные проходы, условные, рабочие и пробные давления для труб, арматуры и соединительных частей трубопроводов. Под условным проходом для трубопроводных элементов понимают номинальный внутренний диаметр в миллиметрах. Для арматуры условный проход равен фактическому внутреннему диаметру. Выбор труб, деталей соединения, фасонных частей и арматуры на основе условного прохода обеспечивает конструктивное соответствие их при комплектовании в трубопровод. Размеры условных проходов регламентированы СТ СЭВ 254—76. Данный стандарт устанавливает следующие условные проходы: 10; 15; 20; 25; 32; 40; 50; 65; 80; 100; 125; 150; 200; 250; 300; 350; 400 и др. Условный проход сокращенно обозначается Dy с добавлением его цифрового значения в миллиметрах, например Dy150.
При гидравлических расчетах трубопроводов их внутренние диаметры обычно принимают равными диаметрам условных проходов. Зная условный проход и толщину стенки трубы, подбирают по государственному стандарту ее наружный диаметр. При выборе размера трубы стремятся к тому, чтобы диаметр условного прохода мало отличался от ее внутреннего диаметра. Расхождение между ними не должно превышать 10%. В противном случае гидравлический расчет выполняют по фактическому внутреннему диаметру трубы.
Предположим, что в результате расчетов были установлены: условный проход трубы Dy = 150 мм и толщина стенки ее s = 5 мм. При данных Dy и s наружный диаметр трубы составит dн = Dy + 2s = = 150 + 2×5 = 160 мм. В ГОСТ 10704—76 (трубы стальные электросварные) имеются трубы с наружным диаметром dH, равным 159 и 168 мм. Выбираем трубу с dH = 159 мм. Внутренний диаметр ее будет dB = dH — 2s = 159 — 2×5 = 149 мм, т. е. на 1 мм меньше расчетного.
Толщина стенки металлической трубы, находящейся под внутренним давлением (мм), должна быть не менее определяемой по формуле
s= so+b+c (1)
где sо— толщина стенки, получаемая из расчета трубы на прочность, мм;
b — прибавка, учитывающая утонение трубы при гибке, мм;
с — прибавка на коррозию, мм.
При определении толщины стенки (мм) пользуются формулой
So =pdн/(2sдj+p) (2)
где р — расчетное давление, принимаемое равным наибольшему давлению
перемещаемой среды в трубопроводе, МПа;
da — наружный диаметр трубы, мм;
σд — допускаемое напряжение на растяжение, МПа, принимаемое для стальных труб равным /2,7 (
— минимальный предел прочности при 20°С, МПа), для медных труб при температуре среды до 100 °С — 40 МПа и для труб из алюминиевой бронзы — 78 МПа;
φ — коэффициент прочности, принимаемый равным 1 для бесшовных труб и 0,9 — для стальных сварных (если сварные трубы признаны эквивалентными бесшовным, то φ — 1).
Если отсутствуют значения фактических утонений трубы при гибке, прибавка на утонение (мм) может быть определена по формуле
где R — средний радиус гиба трубы, мм.
Прибавку на коррозию с принимают (мм):
Для трубопроводов пресной воды.............................................. 0,8
» грузовых и зачистных трубопроводов . .......................... 2
» маслопроводов......................................................................... 0,3
» трубопроводов сжатого воздуха......................................... 1
» трубопроводов хладагента …………………………………. 0,3
для паропроводов....................... ……………………………. 0,8
» змеевиков для подогрева воды и нефтепродуктов в цистернах
и грузовых танках....................... …………………………… 2,0
Примечание. Для труб из специальных стальных сплавов, обладающих достаточной коррозионной стойкостью, прибавка с может быть уменьшена или вообще не учитывается.
Для медных и латунных труб прибавку с принимают равной 0,8 мм.
В случае применения труб, имеющих минусовый допуск на толщину при изготовлении, толщину их стенки следует определять по формуле.
s1=s/(l—а/100), (3)
где s — толщина стенки трубы, вычисленная по формуле (1);
а — минусовый допуск на толщину трубы, %.
Рассчитанную по формуле (1) или (3) толщину стенки нужно округлять до ближайшего большего размера, предусмотренного соответствующим стандартом на трубы. Допускается принимать ближайший меньший размер толщины стенки, если он отличается от найденного не более чем на 3% . Необходимо отметить, что при давлениях в трубопроводах менее 1 МПа толщину стенки часто принимают без проверки на прочность по прототипу, исходя из условия долговечности и необходимой жесткости во время монтажа.
Согласно Правилам Регистра минимальные толщины стенок труб из углеродистой стали для различных сред должны приниматься по табл. 2, если подсчитанные по формуле (1) или (3) толщины стенок труб будут меньше указанных в таблице.
Важным параметром для труб и других трубопроводных элементов является давление ру. Под ним понимается наибольшее допустимое давление в трубе при постоянном условном значении температуры среды. По условному давлению подбирают арматуру трубопровода. Условное давление служит критерием для выбора рабочего давления pv, которое представляет собой наибольшее допустимое давление среды, перемещаемой в трубе при действительной рабочей температуре. Давление, которое должна выдержать труба при гидравлическом испытании, называется пробным рпр. Условные, пробные и рабочие давления регламентированы СТ СЭВ 254—76. Согласно данному стандарту арматура и соединительные части трубопроводов должны изготовляться на следующие избыточные условные давления (МПа): 0,1; 0,25; 0,4; 0,6; 1,0; 1,6; 2,5; 4,0 и др. Для труб, арматуры и соединительных частей трубопроводов из углеродистой стали условное давление равно допускаемому рабочему давлению рр при температуре среды до 200° С, а для труб, арматуры и соединительных частей трубопроводов из чугуна, меди, бронзы и латуни — при температуре до 120°С. Значение пробного давления примерно в 1,5 раза больше условного давления, т. е. рпр ≈ 1,5 ру. СТ СЭВ 254—76 не распространяется на трубопроводы в собранном виде.
Многие трубы судовых систем выполняют с изгибами. Согласно требованиям Правил Регистра стальные, медные и алюминиевые трубы, работающие под давлением более 0,5 МПа или проводящие среду, температура которой выше 60°С, должны иметь внутренний радиус гиба не менее 2,5 dn (dH — наружный диаметр трубы). При работе труб в иных условиях и при использовании машинной гибки радиус гиба их может быть уменьшен до 1,5 д.ъ (dB — внутренний диаметр трубы).
Таблица 2
Назначение трубопровода | Наружный диаметр трубы, мм | ||||||||||
76 | 89 | |||||||||||
Толщина стенки, мм | |||||||||||
Воздушные, переливные, измерительные трубы цистерн Трубопроводы забортной воды (осушительные, балластные и др.) Грузовые и зачистные трубопроводы, змеевики для обогревания нефтепродуктов | 2,5 2,5 | 2,5 | 2,5 4,5 | 3,2 3,5 | 3,2 3,5 | 5,6 | 4,5 4,5 | 6,3 6,3 | |||
Примечание.Толщины для измерительных труб относятся к участкам труб, расположенным вне цистерн, для которых они предназначены.
После окончательной обработки в цехе (гибки, сварки) трубы подвергают гидравлическому испытанию на прочность по нормам Регистра. Смонтированные на судне трубопроводы подвергают гидравлическому испытанию на плотность соединений на следующие давления, МПа (извлечение из Правил Регистра):
Приемные осушительные и балластные, проходящие
через цистерны .............................................. ………………….0.4
Приемные осушительные и балластные, не проходящие
через цистерны………………………………………………………0,2
Напорные водяные трубопроводы.................. ………………….1,2p*р
Грузовые и зачистные напорные трубопроводы………………1,25р ,
но не менее 0,4
Змеевики подогрева жидкого груза…………………………….1,5р*,
но не менее 0,4
_______
* рр — рабочее давление в данном трубопроводе, МПа.
Испытания воздушных, переливных и измерительных труб должны производиться давлением, равным давлению испытания цистерн, к которым они подведены.
ПУТЕВЫЕ СОЕДИНЕНИЯ ТРУБОПРОВОДОВ
При монтаже трубопроводов на судне приходится соединять трубы между собой, а также с арматурой, механизмами и другим оборудованием. Для этого используют соединительные детали, которые обычно называют путевыми соединениями, или соединительной арматурой.
Соединения труб бывают разъемными и неразъемными. К разъемным относят: фланцевые, штуцерно-торцевые, фитинговые и дюритовые соединения, а к неразъемным — сварные и паяные. В судовых системах главным образом применяют разъемные соединения. Они позволяют во время эксплуатации и ремонта системы разбирать и собирать трубопровод. Неразъемные соединения получили распространение на участках трубопроводов, расположенных в труднодоступных местах и не требующих разборки в обычных условиях работы системы.
Рассмотрим конструктивное устройство разъемных соединений.
Фланцевые соединения. Они встречаются в судовых системах наиболее часто. Как правило, их применяют для труб с условным проходом Dy ≥ 32. Фланцевые соединения бывают самых разнообразных конструкций. В судовых системах широкое распространение получили фланцы, показанные на рис. 3. Плоский приварной стальной фланец (рис. 3, а) прост по конструкции и надежен в работе. Такие фланцы выполняют для условных давлений ру до 1,6 МПа. Свободные фланцы (рис. З, б, в) в отличие от приварных можно легко поворачивать на трубе для совмещения отверстий при постановке болтов, что облегчает монтаж трубопроводов. Фланцы на приварном стальном кольце (см. рис. 3, б) применяют для ру до 1,6 МПа, а на отбортованной стальной трубе (см. рис. 3, в) — для ру до 1 МПа. Для стальных и медных труб фланцы изготовляют из стали, а для труб из алюминиевых сплавов— из алюминиевого сплава АМг5В. Применение свободных стальных фланцев на отбортованных медных трубах позволяет экономить цветной металл. Фланцы можно также крепить к трубе с помощью резьбы. В этом случае фланец, имеющий внутреннюю нарезку, навертывают на нарезанный конец трубы. Такие фланцы применяют для трубопроводов, выполняемых из водогазопроводных труб. Для соединения полиэтиленовых труб используют свободные фланцы из текстолита или винипласта.
![]() |
![]() |
![]() | |||
![]() |
Чтобы обеспечить плотность соединения, между соприкасающимися поверхностями металлических фланцев 1 устанавливают прокладку 3 в виде кольца (рис. 3, г), а на поверхностях делают круговые проточки (две-три) глубиной не более 1 мм. Качество уплотнения фланцев зависит от их пригонки, материала прокладок, правильности сборки и равномерности обжатия. Материал прокладок выбирают в зависимости от рода и параметров протекающей по трубопроводу среды. Цифрами на рис. 3, г обозначены: 2 — труба; 4 — болт.
Для водопроводов при температуре воды 30—50 °С обычно применяют прокладки из резины, прессшпана и прокладочного картона. Если вода питьевая, то прокладки выполняют из очищенной (пищевой) резины. В водопроводах горячей воды используют прокладки из теплостойкой резины или паронита. Прокладки для паропроводов изготовляют из паронита. Такие же прокладки получили распространение в воздухопроводах при давлении воздуха до 5 МПа. В нефтепроводах применяют прокладки из прессшпана, нефтестойкой резины, пластиката хлорвинилового специального. Если транспортируемой средой является углекислота, то прокладки делают из фибры КГФ или меди. В трубопроводах, по которым протекает фреон, ставят медные прокладки.
Штуцерно-торцевые соединения. Их используют в трубопроводах с малыми условными проходами (Dy 34-32) при давлениях до 10 МПа. Конструктивное устройство таких соединений показано на рис. 4. Необходимая плотность их обеспечивается прокладкой 2, зажимаемой накидной гайкой 3 между штуцером 4 и ниппелем 1,приваренными к трубам.
Материалом штуцерно-торцевых соединений для пресной воды, воздуха, пара и нефтепродуктов служит углеродистая сталь. Для морской воды соединения выполняют из бронзы или латуни.
Прокладки для штуцерно-торцевых соединений изготовляют из паронита. Перед установкой их покрывают слоем графита.
Фитинговые соединения. Для соединения водогазопроводных труб на резьбе применяют фитинги (угольники, муфты, тройники, четверники) из стали или ковкого чугуна. На рис. 5 показаны фитинговые соединения труб с помощью резьбовой муфты и угольника, с внутренней резьбой на обоих концах.
При муфтовом соединении (рис. 5, а) на конце одной трубы нарезается удлиненная резьба (сгон) для муфты 2 и контргайки /, на конце другой трубы — резьба длиной, равной примерно половине длины муфты. Трубы соединяют путем свинчивания муфты со сгона на другой конец трубы до конца (сбега) резьбы. Для обеспечения необходимого уплотнения в резьбе подматывают паклю или лен на сурике или белилах и поджимают контргайку.
Соединение с помощью угольника (рис. 5, б) осуществляется путем завертывания его на конце труб, предварительно смазанных суриком, с применением подвивки льняного волокна, пропитанного суриком.
Для фитинговых соединений применяется круглая и цилиндрическая резьба. Данные соединения используют для трубопровода диаметром D у ≤ 50 при рабочем давлении до 0,5 МПа.
Дюритовые соединения. В состав этих соединений входят эластичная муфта 2 из резинотканевого материала и обжимные металлические хомутики 3 (рис. 6). В качестве муфты может быть использован, например, отрезок резинотканевого шланга. Цифрой 1 на рис. 6 обозначена труба. К существенному недостатку дюритовых соединений следует отнести непродолжительный срок их службы (2—3 года). Регистр разрешает применять дюритовые соединения только в виде патрубков, соединяющих трубопроводы с двигателями и механизмами, установленными на амортизаторах.
ФАСОННЫЕ ЧАСТИ ТРУБОПРОВОДОВ
Для присоединения ответвлений трубопроводов служат фасонные части: литые колена (рис. 7, а), литые (рис. 7, б) и сварные (рис. 7, в) тройники, крестовины и др. Их изготовляют сварными или литыми. Чтобы обеспечить непроницаемость судовых конструкций, в местах прохода через них труб
![]() |
![]() |
устанавливают переборочные стаканы с приварышами (рис. 7,г).
Переборочный стакан крепится к приварышу 2 средним фланцем 1, а для того чтобы концевой фланец 3 прошел через переборку, в последней делается отверстие диаметром несколько большим, чем его диаметр. С помощью приварыша не только крепят переборочные стаканы, но и непосредственно соединяют трубы и арматуру со стенками цистерн и других конструкций.
Кроме фасонных частей, в трубопроводах применяют компенсаторы, служащие для восприятия температурных удлинений или возможных смещений труб, вызываемых деформацией судовых конструкций. Компенсаторы как самостоятельные детали монтируют только в трубопроводах больших диаметров и длин. Для большинства же систем в качестве их используют изогнутые участки труб (самокомпенсаторы). К элементам судовых конструкций трубы крепят с помощью подвесок и опор (кронштейнов) из полосовой или профильной стали, охватывающих одну или несколько близко расположенных труб.
АРМАТУРА
Чтобы каждая система на судне могла выполнять свои функции, на трубопроводах системы размещают арматуру, с помощью которой осу-ществляют пуск ее в действие, включают и выключают отдельные участки трубопроводов, изменяют режим работы системы, регулируют давление среды, протекающей в трубопроводах, и т. п.
Классификация арматуры может быть проведена по различным признакам. Наибольшее распространение получила классификация по назначению. В этом случае арматуру судовых систем подразделяют на следующие основные типы: запорно-переключающая — клапаны, задвижки (клинкеты), краны, клапанные коробки; предохранительная— предохранительные клапаны, приемные сетки, фильтры; арматура пропускающая среду только в одном направлении, — невозвратные и невозвратно-запорные клапаны, захлопки; регулирующая — редукционные и дроссельные клапаны, манипуляторы; специальная — кингстоны, пожарные рожки (краны), донные клинкеты и др.
По способу изготовления арматура бывает литая, сварная и штампованная. Арматуру судовых систем выполняют из чугуна, стали и цветных сплавов (бронзы различных марок, латуни). Для арматуры, работающей в морской воде, широко применяют алюминиево-марганцовистую бронзу марки АМц9-2. Отдельные детали (тарелку, седло) стальной и чугунной арматуры целесообразно изготовлять из цветных сплавов. Начали использовать и пластмассовую арматуру, которая значительно легче металлической и может работать в агрессивных средах.
В зависимости от типа соединений с трубами арматура разделяется на фланцевую, штуцерную, муфтовую и с присоединением под дюрит. Различают также арматуру, действующую автоматически (невозвратные, предохрани-тельные и редукционные клапаны), и приводную, которая выпускается
Рис.8. Запорно-переключающая арматура
![]() | ![]() | ||
с ручными и механизированными приводами (см. п. 9).
Ниже приводятся некоторые примеры конструкций типовой арматуры судовых систем. Специальная арматура рассматривается совместно с системами в которых она применяется.
Запорно-переключающая арматура. С помощью ее включают, отключают и переключают трубопроводы и механизмы систем (рис. 8).
Клапаны (рис. 8, а) относят к наиболее распространенной запорной арматуре. Запор в них осуществляется тарелкой 9, прижимаемой шпинделем 5 к уплотнительным поверхностям 10 н 11 ъ тарелке и корпусе / клапана. При вращении маховика 3 шпиндель благодаря нарезке на его наружной поверхности и неподвижной втулке 4 с внутренней нарезкой перемещается относительно корпуса клапана и поднимает или опускает тарелку. Чтобы обеспечить герметичность, в месте прохода шпинделя через крышку 2 корпуса клапана установлен сальник, состоящий из нажимной втулки 6, набивки 7 и опорного кольца 8.
Для контроля за положением тарелки в корпусе клапана имеется указатель хода, перемещающийся между рисками О и 3, которые соответствуют полному открытию или закрытию клапана.
В целях образования уплотнительных поверхностей у клапанов из углеродистой стали производят наплавку специальными сталями (например, 2Х13) или в тарелку и корпус вставляют кольца из бронзы или нержавеющей стали. У стального клапана уплотнительные поверхности выполнены наплавкой. Тарелку у чугунных клапанов часто изготовляют из бронзы. Уплотнительную поверхность в корпусе клапана (седло) делают в виде бронзового вставного кольца. Тарелки из бронзы применяют и в стальных клапанах. На трубопроводах клапаны всегда устанавливают таким образом, чтобы внутреннее давление жидкости в трубопроводах приходилось под тарелку клапана. В этом случае обеспечивается герметичность сальника при закрытом клапане.
По направлению движения потока жидкости клапаны разделяют на проходные и угловые. В проходных клапанах направление движения потока жидкости до и после них не изменяется, в угловых же за клапаном оно изменяется на 90° по отношению направления движения потока жидкости перед клапаном. Угловые клапаны оказывают большее сопротивление протеканию жидкости, чем проходные.
Задвижки имеют затвор в виде диска (клина или шибера). В судовой практике наибольшее распространение получили задвижки с клиновидным диском (рис. 8, б), называемые обычно клинкетами. Проход в клинкете закрывается клином 2, который прижимается к уплотнительным поверхностям, сделанным в корпусе клинкета 1. Поднимается и опускается клин с помощью ходовой гайки 3 и шпинделя 4, приводимого во вращение рукояткой 10. Ходовая гайка при вращении шпинделя получает поступательное движение вверх или вниз, увлекая за собой клин. При верхнем положении клин размещается в нише 11, образуемой корпусом и крышкой 5 клинкета. Герметичность места прохода шпинделя через крышку корпуса клинкета обеспечивается сальником, состоящим, как и у клапана (см. рис. 8, а), из опорного кольца 6, набивки 7 и втулки 8. Задвижка снабжена указателем положения («Открыто» и «Закрыто») 9. Клинкеты имеют меньшее гидравлическое сопротивление и меньшие размеры, чем клапаны с такими же условными проходами, однако уступают им в плотности перекрывания трубопровода из-за трудности пригонки клина к уплотнительным поверхностям корпуса клинкета. Поэтому их применяют при умеренных давлениях протекающей среды.
Рис. 9. Схема возможных переключений кранов различных типов
Используют клинкеты в трубопроводах с условным проходом Dу > 50.
Краны относятся к такой запорно-переключающей арматуре, в корпусе которой есть пробка с одной или несколькими прорезями различной формы. С помощью конусной пробки 6, установленной в корпусе 1 и поворачиваемой рукояткой 3, кран (рис. 8, в) перекрывает трубопровод. Для прохода жидкости в пробке и корпусе крана сделаны отверстия а. В целях обеспечения герметичности пробка плотно притирается к корпусу крана. Последний имеет сальник, состоящий из втулки 2, набивки 4 и опорного кольца 5.
По конструктивному исполнению краны делят на проходные, трехходовые и манипуляторы. Принципиально они отличаются числом и формой прорезей в пробке. На рис. 9 приведены схемы этих прорезей для различных типов кранов, а также показаны их рабочие положения при повороте пробки. У проходного крана в пробке одна прорезь. При двух рабочих положениях пробки он перекрывает и сообщает трубопровод. Трехходовые краны с L- или Т-образной прорезью в пробке при нескольких ее рабочих положениях обеспечивают различные переключения движения жидкости по трем трубкам, подключенным к корпусу крана. В нижней части рисунка показаны различные переключения манипулятора. Как видно, при четырех рабочих положениях пробки с тремя фигурными прорезями возможно движение жидкости по четырем трубкам, подключенным к корпусу крана. Манипулятор от крана отличается тем, что он обеспечивает только переключения направления движения жидкости и не служит для перекрывания трубопроводов. Урановый манипулятор относится к регулирующей арматуре.
Краны имеют ряд преимуществ по сравнению с другой арматурой: быстрота переключения, малое гидравлическое сопротивление. Кроме того, один многоходовый кран при работе может заменить несколько клапанов. Однако из-за трудности обеспечения плотности между проб-сой и корпусом их применяют в трубопроводах с условным проходом Dy < 80 при давлении р < 1 МПа. При Dy25 краны изготовляют преимущественно с муфтами.
Особый вид запорно-переключающей арматуры представляют собой клапанные коробки. Они состоят из нескольких клапанов (двух— шести), размещенных в общем корпусе (рис. 10). Аналогичным образом устроены крановые коробки.
![]() |
Предохранительная арматура. Чтобы предотвратить повышение давления в трубопроводе сверх нормального, в отдельных системах устанавливают
![]() |
предохранительные клапаны (рис. 11), состоящие из корпуса 1, тарелки 7, прижимаемой к седлу 8 через шток 6 цилиндрической пружиной 4, и нажимной втулки 3 для поджатия пружины. Клапан работает автоматически. Как только по какой-либо причине давление в трубопроводе превысит установленное, клапан откроется и пропустит некоторое количество жидкости из области повышенного давления в область меньшего давления (например, в атмосферу). После выхода части жидкости из трубопровода и понижения давления в нем до нормального клапан закроется. Такой клапан предохраняет трубопровод от разрушения при случайных повышениях давления в нем сверх допустимого рабочего. Отрегулированный на определенное давление предохранительный клапан пломбируют. Для постановки пломбы скоба 2 снабжена ушком 5.
В целях уменьшения утечки жидкости шток в месте прохода через крышку имеет выточки, чередующиеся с выступами, которые в совокупности образуют лабиринтовое уплотнение. Пропускная способность предохранительного клапана должна быть такой, чтобы давление в трубопроводе не могло превысить 1,1 рабочего.
Чтобы предотвратить попадание посторонних предметов (обтирочных концов и др.) в механизмы и путевую арматуру, на концах всасывающих труб устанавливают приемные сетки или грязевые коробки. В некоторых системах для очистки рабочей среды применяют фильтры. Устройство этих элементов рассматривается в системах, в которых они используются.
Арматура, пропускающая среду только в одном направлении.
В трубопроводах систем, где требуется обеспечить движение жидкости только в одном заданном направлении и одновременно предотвратить ее движение в обратном направлении, устанавливают арматуру, показанную на рис.12.
Невозвратный клапан (рис. 12, а) не имеет шпинделя и работает автоматически, пропуская среду в одном направлении — под тарелку. Основными деталями его являются корпус 1, крышка 2 и тарелка 3 с направляющим стаканчиком. Поступающая под тарелку жидкость своим давлением поднимает тарелку и проходит в трубопровод над клапаном. При движении жидкости в обратном направлении клапан закрывается под действием давления жидкости на тарелку и собственной массы последней.
Невозвратно-запорные клапаны (рис. 12, б) применяют в тех случаях, когда необходимо обеспечить одностороннее движение жидкости и полностью перекрыть трубопровод. В корпусе 1 клапана расположены тарелка 6 и шпиндель 5, которые не соединены между собой. Шпиндель хвостовиком свободно входит в вертикальное отверстие тарелки. Таким образом, если вращением маховика 3 поднять шпиндель, то тарелка будет работать автоматически, "как у невозвратного клапана, обеспечивая одностороннее движение жидкости. Для перекрывания трубопровода вращением маховика опускают шпиндель и прижимают им тарелку к седлу клапана, как показано на рисунке. Герметичность места прохода шпинделя через крышку 2 корпуса клапана обеспечивает сальник 4.
Захлопка (рис. 12, в) используется в качестве невозвратно-запорного устройства. Рабочим органом ее является тарелка (захлопка) 5, шарнирно закрепленная на валике 4. Корпус 1 захлопки имеет обычный круглый 2 и фасонный бортовой 6 фланцы. В верхней части корпуса находится крышка 3. Захлопка открывается под действием давления протекающей среды или с помощью привода.
Регулирующая арматура (редукционные и дроссельные клапаны, манипуляторы). Она служит для регулирования направления течения или давления рабочей среды.
Редукционный клапан (рис. 13, а) предназначен для снижения (редуцирования) давления жидкости и автоматического поддержания его на заданном уровне. Он состоит из корпуса 1, тарелки 2, связанной штоком с поршнем 3, который соединен с диафрагмой 4. Сверху над диафрагмой находится цилиндрическая пружина 5; сила натяжения пружины регулируется винтом 6. Конструкция клапана позволяет автоматически редуцировать давление жидкости до требуемого значения независимо от изменения его перед клапаном. Допустим, "что при давлении рх перед клапаном размер щели между тарелкой и седлом обеспечивает понижение давления до р2. Если давление Рг перед клапаном увеличится, то, следовательно, повысится давление р2 за ним, которое по косому каналу а передастся на диафрагму, сожмет пружину и поднимет тарелку. В результате этого давление р.2 за клапаном уменьшится до первоначального значения. Если же давление р1 до клапана уменьшится, то понизится давление р2 за клапаном, вследствие чего под действием пружины он опустится, увеличивая проточную часть. При этом давление за клапаном возрастет до заданного значения.
![]() | ![]() |
Дроссельный клапан (рис. 13, б) служит для снижения давления протекающей через него среды. В корпусе 2 клапана размещается тарелка 1, закрепленная на шпинделе 3, имеющем в верхней части
![]() |
Рис 13. Регулирующая арматура
нарезку. Шпиндель проходит через крышку 4 и фиксируется в требуемом положении стопорной гайкой 6. На выступающий конец шпинделя навинчивается колпачок 5. При подъеме тарелки между нею и внутренней поверхностью корпуса клапана образуется щель. Давление за клапаном понижается вследствие увеличения скорости движения жидкости при проходе через щель. Высоту подъема тарелки регулируют вручную. После установки ее в необходимое положение шпиндель фиксируют стопорной гайкой. Дроссельным клапаном можно плавно регулировать давление среды в широком диапазоне. Однако в отличие от редукционного он автоматически не поддерживает давление постоянным при изменении режима работы системы.
Принцип действия кранового манипулятора описан выше.
ПРИВОДЫ АРМАТУРЫ
Запорно-переключающей арматурой, находящейся в доступных местах, управляют с помощью маховиков или рукояток, имеющихся на арматуре. Для управления арматурой, расположенной в недоступных местах, используется привод. Его монтируют в удобном для обслуживания месте. Приводы применяют и в тех случаях, когда пост управления арматурой находится от нее на значительном расстоянии (дистанционное управление). В связи с этим приводы управления арматурой делят на местные и дистанционные. Местные приводы обычно выполняют ручными, а дистанционные — ручными или механизированными. Дистанционные приводы бывают валиковые, пневматические, гидравлические и электрические, а местные — валиковые.
Приводы должны отвечать следую-щим основным требованиям: обеспечивать контроль за открытием и закрытием арматуры; исключать само-произвольное открытие и закрытие ар-матуры; допускать в случае необ-ходимости использование резервных средств управления; элементы приво-дов не должны нарушать непрони-цаемости настилов судовых перекры-тий, через которые они проходят. Валиковый привод получил свое название от валиков, составляющих в совокупности с шарнирами и зубчатыми передачами цепь управ-ления. В качестве валиков обычно при-меняют трубы с наружным диаметром от 15 до 45 мм. Схема валикового привода показана на рис. 14. |
![]() | ||
Рис. 14. Схема дистанционного привода ручного управления арматурой: 1-шарнир; 2 - палубная втулка; 3 — ключ управления приводом; 4 подвеска; 5 — труба (валик); 6—подвеска с шестернями |
|
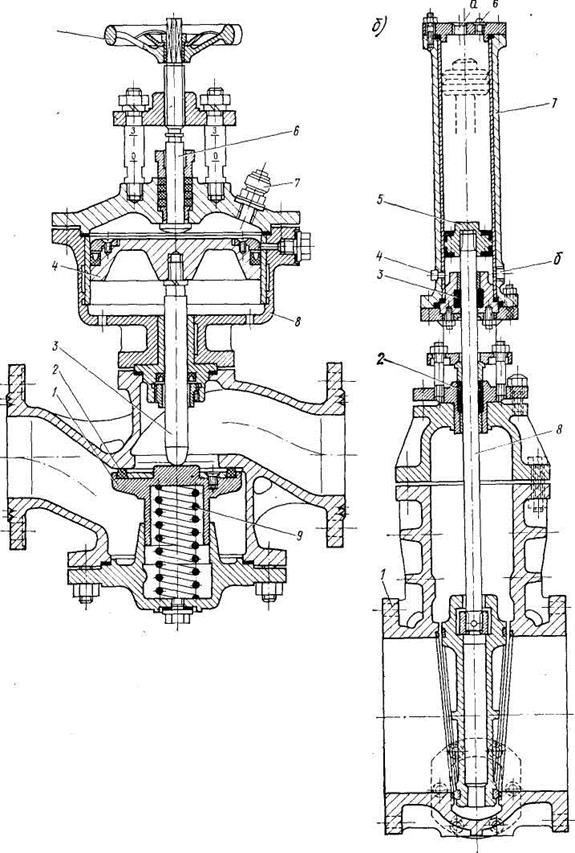
Рис. 15. Дистанционно-управляемая арматура
Клапан с пневмоприводом изображен на рис. 15, а. При подаче сжатого воздуха через штуцер 7 в верхнюю часть цилиндра 8 поршень 4 перемещается вниз и штоком 3 отжимает тарелку / клапана, преодолевая усилие пружины 9. Чтобы клапан закрылся, выпускают воздух из верхней полости цилиндра. Тарелка под воздействием пружины поднимается при этом вверх, и уплотнительное кольцо 2 садится на седло, возвращая поршень в верхнее положение. Для управления клапаном вручную предусмотрен маховик 5. При его вращении по часовой стрелке шпиндель 6 перемещается вниз и открывает клапан. Как правило, системы пневмопривода не имеют собственных источников получения сжатого воздуха и используют его из системы сжатого воздуха на судне либо непосредственно от магистрали, либо от заранее заполненных им баллонов.
На рис. 15, б показан клинкет с гидроприводом. Силовой гидроцилиндр 7 установлен на корпусе /. В цилиндре перемещается поршень 5, соединенный с клинкетным диском штоком 8. Вход последнего в корпус и гидроцилиндр уплотнен сальниками 2, 3. Для открытия клинкета масло подводится в нижнюю полость цилиндра по каналу б, а для его закрытия — в верхнюю полость по каналу а. Пробки 4 и 6 служат для выпуска воздуха при заполнении системы маслом. В гидроцилиндр масло подается под давлением по трубкам через специальный распределительный орган (золотник). Использование масла в гидроприводах, которое служит рабочей жидкостью, удобно при эксплуатации, поскольку оно является хорошей смазкой для трущихся поверхностей и не вызывает коррозии стальных деталей.
В состав электропривода управления арматурой входит электродвигатель или электромагнит. Электродвигатели применяют для клапанов и клинкетов больших условных проходов, открытие которых требует относительно больших мощностей, а электромагниты - для клапанов малых условных проходов (до Dy 32). Электромагнитный привод имеет небольшой размер, и его удобно размещать в общем с клапаном корпусе. Электромагнитные клапаны применяют преимущественно в системах сжатого воздуха.
Дата добавления: 2015-12-11; просмотров: 5716;