Доступность программирования
Главным требованием к ПЛК всегда была и остается возможность его эксплуатации существующим техническим персоналом и возможность быстрой замены старого оборудования. Поэтому языки программирования компьютеров и встраиваемых микропроцессорных систем управления плохо подходят для программирования ПЛК. Здесь нужны более простые и наглядные языки, позволяющие излагать задачу в близких к применяемым технологиям категориях. Привлечение же к программированию специализированной фирмы неизбежно порождает зависимость, если реализация не является достаточно прозрачной. Сложный язык программирования ПЛК снижает его шансы на конкурентном рынке существенно больше, чем массогабаритные показатели.
Кратко о языках стандарта МЭК 1131-3.
Стандарт МЭК 1131-3 описывает синтаксис и семантику пяти языков программирования ПЛК, - языков, ставших широко известными за более чем
30-летнюю историю их применения в области автоматизации промышленных объектов:
1. SFC (Sequential Function Chart) - графический язык, используемый для описания алгоритма в виде набора связанных пар: шаг (step) и переход (transition). Шаг представляет собой набор операций над переменными. Переход - набор логических условных выражений, определяющий передачу управления к следующей паре шаг-переход. По внешнему виду описание на языке SFC напоминает хорошо известные логические блок-схемы алгоритмов. SFC имеет возможность распараллеливания алгоритма. Однако, SFC не имеет средств для описания шагов и переходов, которые могут быть выражены только средствами других языков стандарта. Происхождение: Grafcet (Telemechanique-Groupe Schneider).
2. LD (Ladder Diagram) - графический язык программирования, являющийс стандартизованным вариантом класса языков релейно-контактных схем. Логические выражения на этом языке описываются в виде реле, которые широко применялись в области автоматизации в 60-х годах. Ввиду своих ограниченных возможностей язык дополнен привнесенными средствами: таймерами, счетчиками и т.п. Происхождение: различные варианты языка релейно-контактных схем
![]() |
(Allen-Bradley, AEG Schneider Automation, GE-Fanuc, Siemens).
3. FBD (Functional Block Diagram) - графический язык по своей сути похожий на LD. Вместо реле в этом языке используются функциональные блоки, по внешнему виду - микросхемы. Алгоритм работы некоторого устройства на этом языке выглядит как функциональна схема электронного устройства: элементы типа "логическое И", "логическое ИЛИ" и т. п., соединенные линиями. Корни языка выяснить сложно, однако большинство специалистов сходятся во мнении, что это не что иное как перенос идей языка релейно-контактных схем на другую элементную базу.
4. ST (Structured Text) - текстовый высокоуровневый язык общего назначения, по синтаксису ориентированный на Паскаль. Самостоятельного значения не имеет: используется только совместно с SFC. Происхождение: Grafcet (Telemechanique-Groupe Schneider).
5. IL (Instruction List) - текстовый язык низкого уровня. Выглядит как типичный язык Ассемблера, что объясняется его происхождением: для некоторых моделей ПЛК фирмы Siemens является языком Ассемблера. В рамках стандарта IEC 1131-3 к архитектуре конкретного процессора не привязан. Самостоятельного значения не имеет: используется только совместно с SFC. Происхождение - STEP 5 (Siemens).
Программный ПЛК
Программные приложения, имитирующие технологию ПЛК на компьютере (оснащенном платами ввода-вывода), получили название программный ПЛК (soft РLC). Программная эмуляция ПЛК удобна тем, что благодаря наличию многозадачной операционной системы можно совместить в одном месте контроллер, среду программирования и систему диспетчерского управления.
Рабочий цикл
Задачи управления требуют непрерывного циклического контроля. В любых цифровых устройствах непрерывность достигается за счет применения дискретных алгоритмов, повторяющихся через достаточно малые промежутки времени. Таким образом, вычисления в ПЛК всегда повторяются циклически. Одна итерация, включающая замер, обсчет и выработку воздействия, называется рабочим циклом ПЛК. Выполняемые действия зависят от значения входов контроллера, предыдущего состояния и определяются пользовательской программой.
По включению питания ПЛК выполняет самотестирование и настройку аппаратных ресурсов, очистку оперативной памяти данных (ОЗУ), контроль целостности прикладной программы пользователя. Если прикладная программа сохранена в памяти, ПЛК переходит к основной работе, которая состоит из постоянного повторения последовательности действий, входящих в рабочий цикл.
Рабочий цикл ПЛК состоит из нескольких фаз.
1. Начало цикла.
2. Чтение состояния входов.
З. Выполнение кода программы пользователя.
4. Запись состояния выходов.
5. Обслуживание аппаратных ресурсов ПЛК.
6. Монитор системы исполнения.
7. Контроль времени цикла.
8. Переход на начало цикла.
В самом начале цикла ПЛК производит физическое чтение входов. Считанные значения размещаются в области памяти входов. Таким образом, создается полная одномоментная зеркальная копия значений входов.
Далее выполняется код пользовательской программы. Пользовательская программа работает с копией значений входов и выходов, размещенной в оперативной памяти. Если прикладная программа не загружена или остановлена, то данная фаза рабочего цикла, естественно, не выполняется. Отладчик системы программирования имеет доступ к образу входов-выходов, что позволяет управлять выходами вручную и проводить исследования работы датчиков.
После выполнения пользовательского кода физические выходы ПЛК приводятся в соответствие с расчетными значениями (фаза 4).
Обслуживание аппаратных ресурсов подразумевает обеспечение работы системных таймеров, часов реального времени, оперативное самотестирование, индикацию состояния и другие аппаратно-зависимые задачи.
Монитор системы исполнения включает большое число функций, необходимых при отладке программы и обеспечении взаимодействия с системой программирования, сервером данных и сетью. В функции системы исполнения обычно включается: загрузка кода программы в оперативную и электрически перепрограммируемую память, управление последовательностью выполнения задач, отображение процесса выполнения программ, пошаговое выполнение, обеспечение просмотра и редактирования значений переменных, фиксация значений переменных, контроль времени цикла и т. д.
Пользовательская программа работает только с мгновенной копией входов. Таким образом, значения входов в процессе выполнения пользовательской программы не изменяются в пределах одного рабочего цикла. Это фундаментальный принцип построения ПЛК сканирующего типа. Такой подход исключает неоднозначность алгоритма обработки данных в различных его ветвях. Кроме того, чтение копии значения входа из ОЗУ выполняется значительно быстрее, чем прямое чтение входа. Аппаратно чтение входа может быть связано с формированием определенных временных интервалов, передачей последовательности команд для конкретной микросхемы или даже запросом по сети.
Если заглянуть глубже, то нужно отметить, что не всегда работа по чтению входов полностью локализована в фазе чтения входов. Например, АЦП обычно требуют определенного времени с момента запуска до считывания измеренного значения. Часть работы системное программное обеспечение контроллера выполняет по прерываниям. Грамотно реализованная система исполнения нигде и никогда не использует пустые циклы ожидания готовности аппаратуры для прикладного программиста все эти детали не важны. Существенно только то, что значения входов обновляются автоматически исключительно в начале каждого рабочего цикла.
Общая продолжительность рабочего цикла ПЛК называется временем сканирования. Время сканирования в значительной степени определяется длительностью фазы кода пользовательской программы. Время, занимаемое прочими фазами рабочего цикла, практически является величиной постоянной.
Существуют задачи, в которых плавающее время цикла существенно влияет на результат, например это автоматическое регулирование - для устранения этой проблемы в развитых ПЛК предусмотрен контроль времени цикла. Если отдельные ветви кода управляющей программы выполняются слишком быстро, в рабочий цикл добавляется искусственная задержка. Если контроль времени цикла не предусмотрен, подобные задачи приходится решать исключительно по таймерам.
Время реакции
Время реакции — это время с момента изменения состояния системы до момента выработки соответствующей реакции. Очевидно, для ПЛК время реакции зависит от распределения моментов возникновения события и начала фазы чтения входов. Если изменение значений входов произошло непосредственно перед фазой чтения входов, то время реакции будет наименьшим и равным времени сканирования (рис. 1.5).
Рисунок 5 – Время реакции ПЛК
Худший случай, когда изменение значений входов происходит сразу после фазы чтения входов. Тогда время реакции будет наибольшим, равным удвоенному времени сканирования минус время одного чтения входов. Иными словами, время реакции ПЛК не превышает удвоенного времени сканирования.
Помимо времени реакции ПЛК, существенное значение имеет время реакции датчиков и исполнительных механизмов, которое также необходимо учитывать при оценке общего времени реакции системы.
Существуют ПЛК, которые реализуют команды непосредственного доступа к аппаратуре входов и выходов, что позволяет обрабатывать и формировать отдельные сигналы с длительностью меньшей длительности рабочего цикла.
Для уменьшения времени реакции сканирующих контроллеров алгоритм программы разбивается на несколько задач с различным периодом исполнения. В наиболее развитых системах пользователь имеет возможность создавать отдельные программы, исполняемые по прерыванию, помимо кода, исполняемого в рабочем цикле. Такая техника позволяет ПЛК существенно форсировать ограничение реакции временем сканирования при небольшом количестве входов, требующих сверхскоростной реакции.
Время цикла сканирования является базовым показателем быстродействия ПЛК. При измерении времени рабочего цикла пользовательская программа должна содержать 1К логических команд. Для ПЛК, поддерживающих стандарт МЭК 61131-3, используют команды на языке IL. Иногда изготовители приводят несколько значений времени цикла, полученных при работе с переменными различной разрядности.
Ориентировочно о скорости обработки различных типов данных можно судить по тактовой частоте и разрядности центрального процессора. Хотя нет ничего удивительного в том, что восьмиразрядные ПЛК не редко оказываются быстрее 32-разрядных при выполнении битовых операций. Объясняется это тем, что в 8-разрядных микропроцессорах более распространена аппаратная поддержка работы с битами. Так, в РС-совместимых процессорах для выделения бита приходится использовать логические команды и циклический сдвиг.
Устройство ПЛК
Аппаратно ПЛК является вычислительной машиной. Поэтому архитектура его процессорного ядра практически не отличается от архитектуры компьютера. Отличия заключены в составе периферийного оборудования, отсутствуют видеоплата, средства ручного ввода и дисковая подсистема. Вместо них ПЛК имеет блоки входов и выходов.
Конструктивно контроллеры подразделяют на моноблочные, модульные и распределенные. Моноблочные, или одноплатные, ПЛК имеют фиксированный набор входов-выходов. В модульных контроллерах модули входов-выходов устанавливаются в разном составе и количестве в зависимости от требуемой конфигурации. Так достигается минимальная аппаратная избыточность. В распределенных системах модули или даже отдельные входы - выходы, образующие единую систему управления, могут быть разнесены на значительные расстояния.
Характерным для современных контроллеров является использование многопроцессорных решений. В этом случае модули ввода - вывода имеют собственные микропроцессоры, выполняющие необходимую предварительную обработку данных. Модуль центрального процессора имеет выделенную скоростную магистраль данных для работы с памятью и отдельную магистраль (сеть) для общения с модулями ввода-вывода.
Еще одним вариантом построения ПЛК является мезонинная технология. Все силовые цепи, устройства защиты контроллера выполняются на несущей штате. Процессорное ядро контроллера, включающее систему исполнения, выполнено на отдельной сменной (мезонинной) плате. В результате появляется возможность составлять несколько комбинаций процессорного ядра и разных силовых плат без необходимости корректировки программного обеспечения. При необходимости процессор можно заменить даже в готовой системе.
Системное и прикладное программное обеспечение
Системное программное обеспечение (СПО) непосредственно контролирует аппаратные средства ПЛК. СПО отвечает за тестирование и индикацию работы памяти, источника питания, модулей ввода-вывода и интерфейсов, таймеров и часов реального времени. Система исполнения кода прикладной программы является составной частью СПО. Система исполнения включает драйверы модулей ввода-вывода, загрузчик кода программ пользователя, интерпретатор команд и отладочный монитор. Код СПО расположен в ПЗУ и может быть изменен только изготовителем ПЛК.
Код прикладной программы размещается в энергонезависимой памяти, чаще всего это электрически перепрограммируемые микросхемы. Изменение кода прикладной программы выполняется пользователем ПЛК при помощи системы программирования и может быть выполнено многократно.
Контроль времени рабочего цикла
Правильно составленная пользовательская программа не должна содержать бесконечных циклов. В противном случае управление системе исполнения не будет передано, и, соответственно, нормальное функционирование контроллера будет нарушено. Для преодоления данной проблемы служит контроль времени цикла. Контроль осуществляется при поддержке аппаратно реализованного сторожевого таймера Если фаза пользовательского кода выполняется дольше установленного порога, то ее работа будет прервана. Таким образом, достигается предсказуемое поведение ПЛК при ошибках в программе и при зависании по причине аппаратных сбоев.
Обслуживание сторожевого таймера выполняется в рабочем цикле ПЛК. Выполнять эту операцию по прерыванию нельзя, поскольку при зависании процессора система прерываний достаточно часто продолжает исправно работать.
Электрические исполнительные механизмы.
Назначение.
Механизмы исполнительные электрические однооборотные постоянной скорости МЭО и МЭОФ предназначены для перемещения регулирующих органов в системах автоматического регулирования технологическими процессами в соответствии с командными сигналами автоматических регулирующих и управляющих устройств.
Принцип работы механизмов заключается в преобразовании электрического сигнала поступающего от регулирующего или управляющего устройства во вращательное перемещение выходного вала.
Сочленение с арматурой:
- механизмы МЭО устанавливаются на специальных площадках вблизи арматуры и связываются с ней посредством тяг и рычагов;
- механизмы МЭОФ устанавливаются непосредственно на арматуру и соединяются с ней с помощью монтажных частей.
Основные функции:
- автоматическое или дистанционное перемещение рабочего органа;
- автоматический и дистанционный останов рабочего органа арматуры в любом промежуточном положении;
- позиционирование рабочего органа трубопроводной арматуры в любом положении;
- ручное перемещение рабочего органа арматуры;
- формирование информационного сигнала о конечных и промежуточных положениях рабочего органа арматуры и динамике его перемещения.
Основные параметры.
Основными параметрами, определяющими типоразмер механизма, являются:
- номинальный крутящий момент на выходном валу в N. m (ньютон на метр);
- номинальное значение полного хода выходного органа в оборотах;
- номинальное значение времени полного хода выходного вала в секундах.
Значения основных параметров механизмов приводятся в каталоге для каждой группы и типоразмера механизма.
Необходимый крутящий момент обеспечивается подбором мощности электродвигателя механизма, передаточного отношения редуктора и его коэффициента полезного действия. Величина крутящего момента определяет габаритные размеры и массу механизма.
Механизмы обеспечиваю фиксацию положения выходного вала при отсутствии напряжения питания.
Пусковой крутящий момент механизмов при номинальном напряжении питания превышает номинальных крутящий момент не менее чем в 1,7 раза.
Люфт выходного вала механизмов это разность положений выходного органа исполнительного механизма при приложении к нему момента (силы) в прямом и обратном направлениях, работающего с установившейся скоростью, с момента включения до полной остановки. Люфт выходного вала механизмов при нагрузке (25 – 27) % значения номинальной нагрузки для механизмов с номинальным моментом до 100 N. M и (5 – 6) % для остальных механизмов не превышает:
- 10 – для механизмов с номинальным моментом на выходном валу до 40 N. M;
- 0,750 – для механизмов с номинальным моментом на выходном валу более 40 N. M.
Степень защиты оболочки механизмов не ниже IP 54 по ГОСТ 14254.
Динамические характеристики механизмов.
Выбег выходного вала – это перемещение выходного органа разность перемещения выходного органа механизма, работающего с установившейся скоростью, с момента включения до полной остановки.
Выбег выходного вала:
- 1 % полного хода выходного вала – для механизмов с временем полного хода не более 15 сек;
- 0,5 % полного хода выходного вала – для механизмов с временем полного хода не более 20 сек и более;
- 0,25 % полного хода выходного вала – для механизмов с временем полного хода не более 50 сек и более.
Электрическое питание механизмов:
- однофазный ток напряжением 220 В частотой 50 Гц; 220, 230, 240 В частотой 60 Гц;
- трехфазный ток напряжением 220/380 В частотой 50 Гц; 220/380, 230/400, 240/415 В частотой 60 Гц.
Электрическое питание блоков сигнализации положения:
Электрическое питание блока БСПТ:
- источник постоянного тока напряжением 24 В и током не менее 0,1 А с отклонениями по напряжению плюс 4 и минус 6 В;
- однофазная сеть переменного тока номинальным напряжением 220 или 230, или 240 В частотой 50 Гц, или 220 В частотой 60 Гц с использованием выносного блока питания БП-20 (БП-10 – в ранее выпускавшихся механизмах), поставляемого в составе механизма;
- однофазная сеть переменного тока номинальным напряжением 220 или 230, или 240 В частой 50 Гц, или 220 В частотой 60 Гц с использованием внутреннего источника питания БП-20 в механизмах МЭО-92Кб.
Электрическое питание блока БСПР:
- сеть переменного тока напряжением до 12 В частотой 50 или 60 Гц;
- сеть постоянного тока напряжением до 12 В.
Электрическое питание блока БСПИ:
- сеть переменного тока напряжением 24 В и током не менее
0,1 А с отклонениями по напряжению плюс 4 минус 6 В;
- однофазная сеть переменного тока напряжением 220 или 230, или 240 В частотой 50 Гц, или 220 В частотой 60 Гц с использованием внешнего блока питания БП-24, не входящего в состав поставки механизма.
Устройство.
Механизмы состоят из следующих основных узлов: электродвигатель, редуктор, блок сигнализации положения, привод ручной. рычаг – в механизмах МЭО, фланец – в механизмах МЭОФ.
Двигатель.
В механизмах используют электродвигатели:
- синхронные низкооборотные с частотой вращения 150 об/мин;
– для механизмов с крутящим моментом до 250 N. m.;
- асинхронные двигатели - для механизмов с крутящим моментом от 250 N. m. до 4000 N. m.
Двигатели обеспечивают повторно-кратковременный режим работы механизмов с частыми пусками
Управление работой механизмов контактное и бесконтактное при помощи пускателей бесконтактных реверсивных ПБР или усилителей тиристорных трехпозиционных. В системах автоматического регултрования в основном используется бесконтактный способ управления как более надежный.
Редуктор.
Редуктор является основным узлом, к которому присоединяются все остальные узлы.
Понижение частоты вращения и увеличение крутящего момента, создаваемых двигателем, осуществляется посредством многоступенчатых цилиндрических или комбинированных червячно-зубчатых передач. валы вращаются на шарикоподшипниках.
Блок сигнализации положения выходного вала.
Предназначен для преобразования положения выходного вала механизма в пропорциональный электрических сигнал, либо изменения активного или реактивного сопротивления в зависимости от типа датчиков. А также для сигнализации и (или) блокирования в крайних или промежуточных положениях выходного вала.
Механизмы оснащают одним из видов блока сигнализации положения выходного вала с датчиком обратной связи (блок датчика): реостатным БСПР, индуктивным БСПИ, токовым БСПТ с унифицированным токовым сигналом. В условном обозначении механизма ставят соответственно следующие буквы - «Р», «И», «У».
1. Реостатный блок сигнализации положения выходного вала механизмов БСПР.
Механизм с блоком БСПР используется в случае достаточно жестких условий эксплуатации механизма – при наличии вибрации, тряски, влажности, отрицательной или высокой положительной температуры, а также в системах управления с небольшой интенсивностью включения.
Рекомендации по эксплуатации механизмов с блоком БСПР:
- допускаемое расстояние между механизмом и шкафом управления – не более 100 м;
- соединительные цепи реостатного датчика для подавления помех должны быть отделены экраном от остальных цепей.
Для визуального указания положения реостатного датчика применяется дистанционный указатель положения ДУП – М. Для преобразования значения положения реостатного датчика в унифицированный сигнал можно использовать нормирующий преобразователь НП – Р10, блок усилителя БУ – 30М или другой нормирующий преобразователь.
Для подачи сигнала реостатного датчика в систему управления он может быть подключен на вход контроллера без использования дополнительных преобразователей.
2. Индуктивный блок сигнализации положения выходного вала механизма БСПИ.
Механизм с блоком БСПИ рекомендуется применять в зонах с повышенными значениями климатических факторов. Применяется в системах управления с режимом работы до 360 включений в час.
Рекомендации по эксплуатации механизмов с блоком БСПИ:
- допускаемое расстояние между механизмом и шкафом управления – не более 100 м;
- соединительные цепи индуктивного датчика для подавления помех необходимо экранировать от других цепей, устанавливать специальные фильтры на входах системы управления.
Для визуального указания положения индуктивного датчика применяется дистанционный указатель положения ДУП – М. Для преобразования значения положения индуктивного датчика в унифицированный сигнал можно использовать нормирующий преобразователь НП – П10, блок усилителя БУ – 30М.
3. Токовый блок сигнализации положения выходного вала механизмов БСПТ.
Механизм с блоком БСПТ применяется в основном во всех системах управления и регулирования АСУ ТП. (Режим работы механизма до 360 включений в час – для МЭО ЗЭиМ).
Допускаемое расстояние между механизмом и шкафом управления до 1000 м. Расстояние определяется величиной нагрузки: не более 2,5 кОм для сигнала 0 – 5 мА; 1 кОм – для сигнала 4 – 20 мА. В блоке имеется микропереключатель вида выходного сигнала (0 – 5 мА или 4 – 20 мА).
Особенности системы управления и условия ее эксплуатации должны учитываться при выборе типа блока сигнализации положения выходного вала механизма (реостатный БСПР, индуктивный БСПИ, токовый БСПТ).
В состав каждого блока сигнализации положений входят два основных узла: блок микропереключателей и блок датчиков. Микропереключатели предназначены для ограничения и сигнализации положения выходного вала, расположены компактно и образуют собственно блок концевых выключателей БКВ.
Блок микропереключателей содержит основание, корпус с 4 микровыключателями
(2 выключателя для ограничения перемещения выходного вала и 2 выключателя для блокирования и сигнализации промежуточных положений выходного вала) и вертикальный вал с кулачками. На вертикальном валу расположены четыре кулачка для воздействия на микропереключатели и один кулачок с двумя профилями по Архимедовой спирали с углами подъема 900 и 2250 (соответственно поворот вала блока – 0,25r (об.) и 0,63r (об.)), который используется для индуктивного и токового блоков сигнализации положения. В реостатном блоке сигнализации вместо профильного кулачка ставится бегунок.
При повороте вала кулачки микропереключателей, в зависимости от положения вала, нажимают на толкатель микропереключателя и вызывают его срабатывание.
В качестве местного указателя положения выходного вала механизмов МЭОФ используются блоки сигнализации положения со шкалой и стрелкой.
Ручное управление.
Ручное перемещение выходного вала механизма осуществляется вращением ручки ручного привода. Полному ходу выходного вала механизма соответствует определенное число оборотов ручного привода.
Действительное время полного хода выходного вала – это время выходного органа с установившейся скоростью, измеренное при номинальном напряжении питания и номинальной противодействующей нагрузке
Регулирующие органы.
Регулирующие органы служат для изменения количества вещества или энергии, подводимых к объекту регулирования или отводимых от него по определенной программе или поддержание на определенном уровне.
Чаще всего с помощью регулирующих органов изменяют расход вещества, подаваемого в объект регулирования. Изменение расхода среды при перемещении регулирующего органа из одного крайнего положения в другое называют диапазоном регулирования органа. Для обеспечения регулирующим органом управления процессом необходимо, чтобы диапазон регулирования его превышал те изменения расхода среды, которые могут иметь место при переходе от минимальной нагрузке к максимальной.
Действие регулирующего органа в пределах диапазона регулирования оценивается его статической характеристикой, т. е. зависимостью расхода среды от положения (степени открытия) регулирующего органа.
Различают теоретическую и рабочую статические характеристики. Теоретическая характеристика определяется при постоянном перепаде давления на регулирующем органе, а рабочая – при переменном перепаде, т. е. для реальных рабочих условий. Рабочая характеристика может отличаться от теоретической. Если последняя линейна, то рабочая характеристика может быть существенно нелинейной. Поэтому для получения линейной рабочей характеристики необходимо выбрать профиль регулирующего органа так, чтобы теоретическая характеристика была нелинейной. Регулирующие органы обычно выполняются с линейной, параболической или логарифмической теоретическими характеристиками.
Чаще других в качестве регулирующих органов используют клапаны (рисунок 6 а).
|
|
|
|
|
|
|
|
|
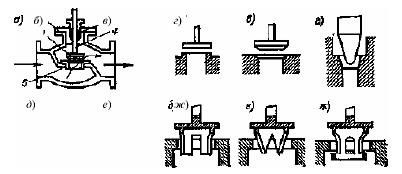
Рисунок 6 - Типы регулирующих клапанов
Регулирование расхода среды через клапан осуществляется за счет изменения проходного сечения между плунжером 1 и седлом 5. Поверхность, по которой соприкасаются плунжер и седло в закрытом положении, называют опорной поверхностью. Шток 4, перемещающийся под действием привода, выведен из корпуса 2 наружу через сальник 3.
Статическая характеристика клапанного регулирующего органа определяется формой и размерами плунжера и седла, которые могут быть различными (рисунок 6 б - ж).
На рисунок 6 б показан тарельчатый клапан с плоской опорной поверхностью. Проходное сечение его – цилиндрическая поверхность. Такие клапаны применяют редко, так как при больших скоростях протекания среды через них кромки тарелок быстро истираются, что приводит к изменению характеристик клапанов.
Тарельчатые клапаны с конической опорной поверхностью (рисунок 6 в) используют для регулирования больших расходов. Проходным сечением у них служит кольцевая щель между внутренней кромкой плунжера и опорной поверхностью седла.
Игольчатые клапаны (рисунок 6 г) применяют для сравнительно малых расходов среды и при значительных давлениях. Проходным сечением игольчатых клапанов служит коническая щель между внутренней кромкой седла и конической поверхностью плунжера.
Золотниковый клапан (рисунок 6 д, е, ж) представляет собой полый цилиндр с прорезанными в его боковой стенке окнами. Величина проходного сечения клапана определяется суммарной площадью той части окон, которая выступает над кромкой седла. Окна могут быть прямоугольного (рисунок 6 д), треугольного (рисунок 6 е) или другого по форме (рисунок 6 ж) сечения.
На рисунок 7 представлены некоторые конструкции регулирующих органов. Они выполняются как односедельными, так и двухседельными.
Односедельные регулирующие органы (рисунок 7 а) применяют для установки на трубопроводах малого диаметра и при небольших перепадах давлений на клапанах. Обычно регулирующие органы исполнительных механизмов выполняют двухседельными прямого (рисунок 7 б, в) или обратного (рисунок 7 г) действия. У регулирующих органов прямого действия при ходе штока вниз проходное сечение уменьшается, а у регулирующих органов обратного действия – увеличивается. Двухседельные клапаны позволяют значительно уменьшить усилие, оказываемое на шток регулирующего органа.
Кроме указанных регулирующих органов для регулирования расхода загрязненных и агрессивных сред применяются диафрагмовые (рис. 7 д) и шланговые (рисунок 7 г) клапаны. В диафрагмовых клапанах проходное сечение перекрывается диафрагмой из специального материала, стойкого к регулируемой среде.
|
|
|
|
|
|
|
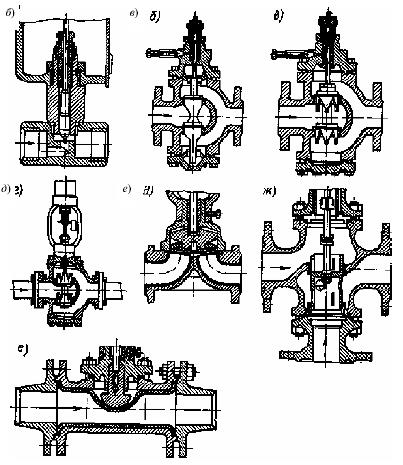
Рисунок 7 - Конструкции регулирующих клапанов
В промышленности последнее время получают распространение трехходовые смесительные клапаны (рисунок 7 ж). Преимущество их заключается в том, что при постоянном давлении потоков можно без применения специальных регуляторов соотношения поддерживать соотношение расходов двух смешиваемых потоков.
В системах регулирования при воздействии на потоки газа и пара находят применение также регулирующие заслонки. Они используются в трубопроводах большого диаметра при небольших избыточных давлениях, где допускаются небольшие потери давления. Заслонки могут работать в среде газов, содержащих твердые частицы, а также в среде сыпучих гранулированных твердых материалов. Изменение проходного сечения регулирующего органа достигается поворотом заслонки под действием пневмопривода.
На рисунок 8 показаны некоторые типы заслонок. Круглые заслонки (рисунок 8 а) устанавливают в трубопроводах, а прямоугольные (рисунок 8 б) – в коробах и газоходах. Заслонки прямоугольного сечения могут выполняться однолопастными (рисунок 8 б), многолопастными с разделительными перегородками (рисунок 8 в) и многолопастными без разделительных перегородок (жалюзи) (рисунок 8 г). Применение многолопастных заслонок позволяет значительно уменьшить усилие пневматического привода требуемое для управления заслонкой.
|
|
|
|
|
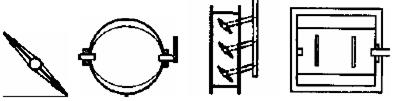
Рисунок 8 - Типы поворотных заслонок
При управлении многими технологическими процессами встречаются задачи регулирования расхода агрессивных или нагретых до нескольких тысяч градусов Цельсия газов и жидкостей, а так же газов и жидкостей, содержащих механические частицы. Установка механических регулирующих органов (клапанов или заслонок) во многих таких случаях невозможна (или неэффективна), так как приводит к быстрому износу регулирующего органа и потере им регулирующей способности. Преодоление указанных трудностей оказалось возможным в некоторых случаях путем применения принципов струйной техники. Первоначально струйные методы были использованы для конструирования исполнительных устройств в ракетно-космической технике.
Дата добавления: 2015-10-05; просмотров: 1299;