Основные превращения в сталях в процессах термообработки
В ходе ТО в сталях структурные превращения происходят при нагреве и охлаждении.
При нагреве осуществляется трансформация ферритно-перлитных, перлитных и перлитно-цементитных структур в аустенит.
В ходе охлаждения происходят обратные превращения:
1. диффузионные изотермические аустенитно-перлитные с различной скоростью;
2. бездиффузионное в мартенсит при остывании аустенита со скоростью выше критической в процессе закалки;
3. в мартенсите при отпуске.
Превращения в сталях при нагреве протекают в соответствии с диаграммой состояния Fe-Fe3C. Однако она дает представление о видоизменениях структур лишь в ходе очень медленного (равновесного) нагрева. В обычных же условиях трансформации протекают при более высоких температурах.
В доэвтектоидных сталях при достижении температуры выше точки Ас1 феррито-цементитная структура, в первую очередь, переходит в аустенитную. Этот процесс заключается в полиморфном видоизменении a « g и растворении цементита (карбида) в образующемся аустените. В интервале температур Ас1 – Ас3 формируется двухфазная структура – аустенит + феррит (g + a). Дальнейший нагрев вызывает трансформацию феррита в аустенит. В ходе процесса концентрация углерода в образующейся структуре уменьшается в соответствии с линией GS на диаграмме (рис. 1.44). При температуре, равной значению в точке Ас3, феррит практически отсутствует, а концентрация углерода в аустените равна его количеству в стали.
Аналогично протекают превращения и для заэвтектоидных сталей. Только аустенит, формирующийся при температурах выше пункта Ас1, содержит 0,8 % С. Область Ас1 – Ас3 характеризуется растворением в аустените избыточного вторичного цементита.
Видоизменение перлита в аустенит – кристаллизационный процесс, который заключается в образовании зародышей аустенита и последующего их роста (рис. 1.46). Зарождение центров аустенитных зерен начинается на поверхности границы раздела феррит – цементит (1). Образовавшиеся зародыши аустенита растут благодаря интенсивной диффузии углерода в структуре, что приводит к растворению карбида в ней и развитию перехода g в a. Одновременно зарождаются новые зерна аустенита (2 и 3). По окончании превращения феррита в формирующейся структуре остается еще некоторое количество цементита, на растворение которого необходимо дополнительное время или повышение температуры (4). С завершением данного процесса структура стали становится однофазной и состоит только из аустенита (5). Однако в первый момент образования он является неоднородным по содержанию в нем углерода. На участках, прилегающих к цементитной составляющей, концентрация неметалла выше, чем в зонах, где располагался феррит. Поэтому на выравнивание концентрации углерода путем его диффузии требуется добавочное время (рис. 1.49).
Рис. 1.49 - Схема изменения структуры эвтектоидной стали в зависимости от температуры
Превращения переохлажденного аустенита. Если сталь аустенитного класса, нагретую выше температуры точки Ас3 или Аст, переохладить до значений ниже Аг1, то система окажется в метастабильном состоянии и будет претерпевать видоизменения. Для описания этих процессов пользуются диаграммами изотермического образования аустенита, протекающего при постоянной температуре. В зависимости от степени переохлаждения различают три температурные области или ступени перехода: перлитную, промежуточную и мартенситную (рис. 1.50).
Перлитное превращение (изотермическое) происходит при таких скоростях охлаждения, когда достигается начало распада аустенита в интервале 700 – 500 °С (скорости V1, V2 и V3). Процесс разложения носит кристаллизационный характер и по своему механизму является диффузионным. Причиной этого является то, что образующиеся фазы резко отличаются от исходной по составу и структуре: феррит (почти чистое железо) и цементит (6,67 % углерода). При этом ведущей структурой, возникающей в первую очередь, является цементит. Как правило, его зародыши образуются на границе зерен аустенита. В результате роста частиц карбида прилегающий к нему слой аустенита обедняется углеродом, снижает свою устойчивость и испытывает полиморфное g ® a превращение. При этом кристаллики феррита зарождаются на границе с цементитом, который облегчает этот процесс. Продолжающийся рост пластинок феррита ведет к обогащению окружающего аустенита углеродом, что затрудняет дальнейшее развитие течения видоизменения g ® a и приводит к зарождению новых и росту ранее возникших пластинок цементита. В результате данного процесса в структуре вновь создаются условия для формирования новых и роста имеющихся зерен феррита. Таким образом, происходит совместный рост кристалликов феррита и цементита, образующих перлитную колонию пластинчатого строения (рис. 1.51).
|
|
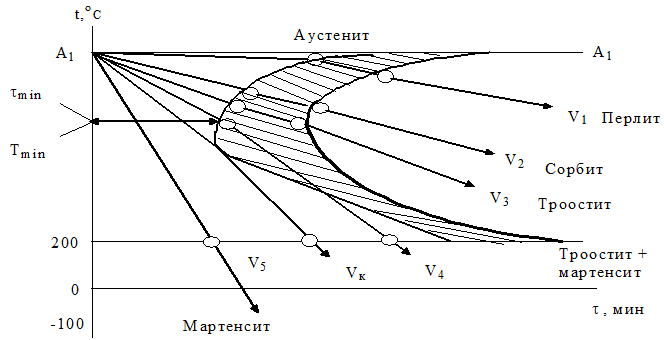
Рис. 1.50 - Диаграмма изотермического превращения аустенита для эвтектоидной стали
Рис. 1.51 - Схема возникновения и роста перлитного зерна: I – аустенит; II – образование зародыша цементита на границе зерна аустенита; III – формирование пластин цементита и феррита; IV – VI - рост и развитие новых пластин перлита; VII – перераспределение углерода при его образовании
Чем больше степень переохлаждения стали, тем тоньше пластинки получающийся перлитной структуры, то есть меньше расстояние (∆0) между пластинками феррита и цементита, включая их толщину, и выше ее твердость. Надо учитывать, что деление феррито-цементитных структур на перлит, сорбит и троостит (П, С и Т) условно. Резкой границы между П, С, Т не существует: по мере понижения температуры постепенно совершается переход от одной структуры к другой. Дело в том, что все они имеют пластинчатое строение и различаются лишь степенью дисперсности (размерами) пластинок (рис. 1.52).
Рис. 1.52 - Микроструктура сталей после нагрева до аустенитного состояния и охлаждения с различными скоростями (V1 – V3), обозначенными на С-образных кривых: а – перлит, б – сорбит, в - троостит
Чем мельче пластинки, тем выше твердость (НВ), пределы текучести (s0,2), выносливости (s-1) и прочности (sв). Относительное удлинение и сужение (d и j) наивысшее у сорбита. При переходе к трооститу пластичность (d и j) уменьшается. Твердость феррито-цементитной смеси прямопропорциональна площади поверхности раздела между ферритом и цементитом. Поэтому с увеличением степени дисперсности фаз повышается их твердость, т. е от перлита к трооститу, а именно 150 у перлита, 200 - сорбита, 250 – троостита и 600 – мартенсита. Диффузионный аустенито-перлитный переход в сталях наблюдается при предварительных видах термической обработки: отжиге и нормализации.
Мартенситное превращение переохлажденного аустенита происходит в том случае, если он быстрым остыванием переохлажден до низких температур, когда диффузионные процессы становятся невозможными из-за очень малой проникающей подвижности ядер. Поэтому данное видоизменение в отличие от перлитного не сопровождается диффузионным перераспределением атомов углерода и железа в структуре. При нем происходит лишь полиморфная трансформация g ® a, заключающаяся в перестройке кубической гранецентрированной решетки в объемно-центрированную, присущую a-железу, без выделения из аустенита атомов углерода. Превращение начинается при определенной температуре, называемой началом мартенситного видоизменения и обозначаемой Мн. Чтобы процесс развивался и не останавливался, необходимо непрерывное охлаждение стали. По достижении определенного значения температуры для каждой марки сплава трансформация прекращается. Эта точка называется концом превращения и именуется Мк Положение пунктов Мн и Мк не зависит от скорости охлаждения и определяется химическим составом аустенита. Чем больше в нем углерода, тем ниже температуры в данных точках. Все легирующие элементы в сталях, за исключением кобальта и алюминия, понижают их значения. Резкое охлаждение создает в металле большие внутренние напряжения. Под их действием в зернах аустенита возникают сдвиговые деформации. В плоскостях смещения подвижность атомов резко возрастает. Поэтому здесь решетка быстро перестраивается. Но избыточный углерод при таком резком перераспределении атомов не успевает диффузионно выделиться из образующейся структуры. Поэтому в данном процессе формируется феррит, пересыщенный углеродом. Вместо объемноцентрированного куба решетка приобретает форму прямоугольного параллелепипеда той же сингонии (рис. 1.53).
Рис. 1.53 - Схема перестройки кристаллической решетки в процессе превращения аустенита в мартенсит
Структурную составляющую такого строения назвали мартенситом. Он имеет большой удельный объем, например, у аустенита с концентрацией углерода 0,2 - 1,4 % составляет 0,12227 - 0,12528 см3/г, а у мартенсита – 0,12708 - 0,13061 см3/г. Это ведет к высокому внутреннему напряжению в сплаве. За счет тонкой неоднородности структуры прочность мартенсита предельно высока, а твердость составляет НВ = 800 МПа (HRC = 60 – 80 ед.). Повышенное внутреннее напряжение предопределяет очень большую хрупкость структуры. В каждом отдельном зерне аустенита сдвиги следуют один за другим. В итоге аустенит превращается в мозаику из пластин мартенсита (рис. 1.54).
Отличительная особенность мартенситного видоизменения – это большие скорости образования и роста кристаллов при низких температурах. Однако зародыши быстро увеличиваются лишь до определенного размера, после чего их рост прекращается. Дальнейшее превращение происходит в результате формирования новых мартенситных центров.
Структура мартенсита низко- и среднеуглеродистых сталей имеет форму реек (реечная), ориентированных в одном направлении (рис. 1.54, а). Чаще всего из них образуется пакет – массивный мартенсит. В высокоуглеродистых сталях по своему строению мартенсит состоит из пластин, имеющих вид игл (рис. 1.54, б). Размеры пластин определяются величинами исходного зерна видоизменяющейся структуры. Первый зародыш мартенсита соответствует поперечнику зерна аустенита. Последующие кристаллы стеснены в своем развитии и имеют меньший размер.
|
|
|
|
|
|
|
|
|
|
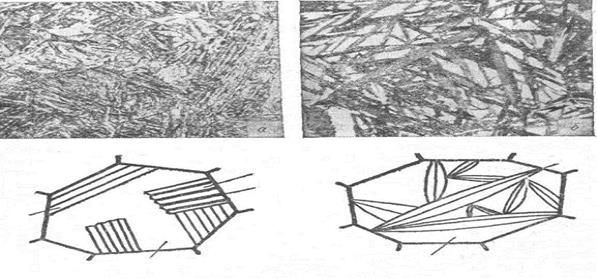
Рис. 1.54 - Микроструктуры, схемы возникновения и роста кристаллов мартенсита: а – реечного; б – пластинчатого (игольчатого). Белые поля – остаточный аустенит
Промежуточное превращение происходит при температурах, лежащих в интервале областей перлитного и мартенситного переходов, когда диффузия железа еще весьма затруднена, а перемещение углерода протекает сравнительно быстро. Поэтому кинетика данного видоизменения и образующаяся структура имеют особенности, складывающиеся из специфики диффузионного перлитного и отличий мартенситного превращений. В результате образуется структура, состоящая из низкоуглеродистого мартенсита и частиц цементита (рис. 1.55). Она называется бейнитом. Главное отличие бейнита от перлитных структур - концентрация углерода в феррите (0,01 - 0,02 % при высоких температурах и 0,1 - 0,2 % при низких). Вблизи границы перлитного превращения в интервале 500 – 350 °С образуется перистый (верхний) бейнит, имеющий структуру троостита. Он состоит из чередующихся коротких пластинок цементита и феррита. При 350 – 250 °С формируется игольчатый (нижний) бейнит, обладающий строением мартенсита. Здесь карбидные частички располагаются внутри пластин a-фазы. Верхний бейнит менее пластичный и более хрупкий по сравнению с продуктами перлитного распада аустенита. При этом твердость (НВ) и прочность (sв, s0,2) не изменяются или лишь незначительно снижаются. Нижний бейнит имеет более высокую твердость и прочность при повышенном сопротивлении разрушению при сопоставлении с сорбитом и трооститом.
|
|
|
|
|
|
|
|
|
|
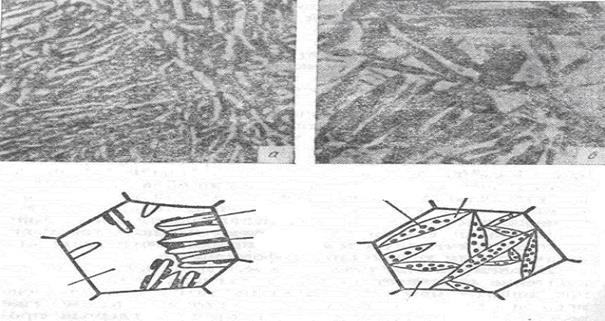
Рис. 1.55 - Микроструктуры и схемы образования верхнего (а) и нижнего (б) бейнита: А – аустенит; М – малоуглеродистый мартенсит; К – карбид; Ф – феррит (пересыщенный углеродом)
Превращение при непрерывном остывании имеет некоторые особенности, связанные с тем, что аустенит переохлаждается до значений температур ниже точки Аг1 и распад его осуществляется не изотермически, а в каком-то интервале. Чем больше скорость охлаждения и меньше температура разложения первоначальной фазы, тем дисперснее будет образующаяся феррито-цементитная структура. При наивысших скоростях остывания (больше чем V3 на рис. 1.50) распад аустенита происходит следующим образом: часть его переохлаждается до температур точки Мн. Структура, формирующаяся в этом случае, состоит из троостита и мартенсита. Иногда ее называют игольчатым трооститом.
Минимальная скорость охлаждения (рис. 1.50, Vкр), при которой весь аустенит переохлаждается до пункта Мн, не подвергаясь диффузионным превращениям, и трансформируется в мартенсит, получила название критической скорости закалки. Для разных сталей значения их различны и зависят от устойчивости аустенита. Чем правее расположены С-образные кривые превращений на диаграмме его изотермического распада, тем ниже критическая скорость закалки
У многих высоколегированных сталей она не превышает 5 – 20 °С/с. Следовательно, некоторые из них подвержены закалке с охлаждением на воздухе (Vкр » 10 °С/с).
Разобранные превращения строения сталей формируют структуры при проведении так называемых высокотемпературных процессов термической обработки: отжига, нормализации и закалки.
1.5.5. Химико-термическая обработка стали. Общая характеристика процессов
Химико-термической обработкой (ХТО) называют поверхностное насыщение стали некоторыми химическими элементами, а именно неметаллами и металлами (например, углеродом, азотом, алюминием, хромом и др.) путем их диффузии в атомарном состоянии из внешней среды при высокой температуре. В ходе данных процессов обязательно изменяется химический состав, микроструктура и свойства поверхностных слоев изделий. При ХТО обрабатываемые детали нагревают в каких-либо химически активных средах. Основные параметры обработки - температура нагрева и продолжительность выдержки. ХТО обычно осуществляется за длительное время. Температуру процесса выбирают конкретно для каждого вида обработки.
Первостепенными процессами любого вида ХТО являются диссоциация, абсорбция и диффузия.
Диссоциация - разложение химического соединения для получения неметаллов в более активном, атомарном состоянии. Абсорбция – поглощение поверхностью детали атомов указанных неметаллов. Диффузия - перемещение абсорбированного элемента в глубь изделия. Скорости всех трех процессов обязательно должны согласовываться друг с другом. Для абсорбции и диффузии необходимо, чтобы насыщающий элемент взаимодействовал с основным металлом с образованием либо твердого раствора, либо химического соединения, так как при отсутствии этого химико-термическая обработка невозможна.
ХТО это стержневой способ поверхностного упрочнения деталей. Основными видами химико-термической обработки являются цементация, азотирование, нитроцементация, цианирование и диффузионная металлизация. Скорость диффузии атомов в решетку железа неодинакова и зависит от состава и строения образующих фаз. При насыщении углеродом или азотом, составляющими с железом твердые растворы внедрения, диффузия протекает быстрее, чем в аналогичном процессе металлами, образующими твердые растворы замещения. Поэтому в данном случае используют более высокие температуры и длительное время обработки, несмотря на это, получают меньшую толщину слоя, чем при азотировании и особенно науглероживании.
Насыщение неметаллами позволяет получать наибольшую толщину диффузионного слоя х, рост которой в зависимости от продолжительности процесса t при данной температуре обычно выражается параболой (рис. 1.56).
|
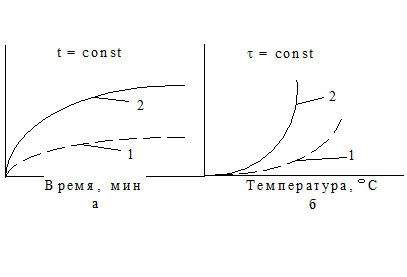
Следовательно, с течением времени скорость увеличения размеров слоя непрерывно уменьшается. Чем выше температура и концентрация диффундирующего элемента на поверхности металла, тем она больше за данный отрезок времени.
При определении толщины диффузионного слоя, полученного при насыщении (стали) тем или иным элементом, обычно указывается не полная его величина с измененным составом, а только глубина до определенной твердости или структуры (эффективная толщина).
Цементацией называется процесс насыщения поверхностного слоя стали углеродом с целью повышения работоспособности деталей металлургических машин (всевозможные шестерни, зубчатые муфты и втулки, пальцы, втулки и ролики шлепперов и т. д.), испытывающих в процессе эксплуатации статические, динамические и переменные нагрузки и подверженных изнашиванию.
При ней изделия, состоящие из низкоуглеродистых сталей (0,10 - 0,18 % С), нагревают в среде, легко отдающей углерод. Для крупногабаритных деталей применяют сплавы с более высокой концентрацией углерода (0,2 - 0,3 %). Выбор таких сталей необходим для того, чтобы сердцевина изделия, не насыщающаяся углеродом при цементации, сохраняла высокую вязкость после закалки.
На цементацию детали поступают после механической обработки нередко с припуском на шлифование 0,05 - 0,10 мм. Во многих случаях науглероживанию подвергается только часть детали, тогда участки, не подлежащие упрочнению, защищают тонким слоем меди (0,02 - 0,04 мм), которую наносят электролитическим способом или изолируют специальными обмазками, состоящими из смеси огнеупорной глины, песка и асбеста, замешанных на жидком стекле, и др.
Цементованный слой имеет переменную концентрацию углерода по глубине, убывающую от поверхности к сердцевине детали. В связи с этим после медленного охлаждения в структуре науглероженного пласта можно различить (от поверхности к сердцевине) три зоны: заэвтектоидную, состоящую из перлита и вторичного цементита, образующего сетку по бывшему зерну аустенита; эвтектоидную из одного пластинчатого перлита и доэвтектоидную из перлита и феррита. За эффективную толщину цементованного слоя обычно принимают сумму заэвтектоидной, эвтектоидной и половины переходной (доэвтектоидной) областей - до 0,40 - 0,45 % С или после закалки толщину до твердости HRC 50 или НV 500 - 600.
Глубиной цементации условно считают расстояние от поверхности изделия до половины зоны, где в структуре наряду с перлитом имеется примерно такое же количество феррита. Толщина цементованного слоя составляет 1 - 2 мм, но может быть и больше. Степень цементации-это средняя концентрация углерода в поверхностном слое (обычно не более 1,2 % С). После цементации изделия подвергают закалке с отпуском. Это обеспечивает получение в поверхностном слое изделий высокой твердости при сохранении мягкой вязкой сердцевины, возникновение напряжений сжатия, увеличивающих предел выносливости и долговечность деталей.
Цементацию проводят в твердом, газообразном и жидком карбюризаторах.
При науглероживании твердым карбюризатором в данном качестве применяется древесный уголь (дубовый или березовый) в зернах размером 3,5 – 10,0 мм. Для ускорения процесса цементации добавляют активизаторы: углекислый барий (ВаСО3) и кальцинированную соду – углекислый натрий (Na2CO3) в количестве 10 – 40 % от массы угля.
Широко применяемый карбюризатор состоит из древесного угля, 20 – 25 % ВаСО3 и до 3,5 % СаСО3. Рабочую смесь для цементации составляют из 25 – 35 % свежего карбюризатора и 65 – 75 % отработанного; концентрация карбоната бария в такой смеси колеблется в интервале 5 – 7 %.
Изделия, подлежащие цементации, после предварительной очистки укладывают в ящики: сварные стальные или реже литые чугунные прямоугольной или цилиндрической формы. При упаковке на дно ящика насыпают и утрамбовывают слой карбюризатора толщиной 20 – 30 мм, на который укладывают первый ряд деталей, выдерживая расстояния между ними и до боковых стенок ящика 10 – 15 мм. Слой изделий засыпают карбюризатором, который хорошо трамбуют. Так поступают по всей высоте ящика. Последний (верхний) ряд деталей засыпают слоем карбюризатора толщиной 35 – 40 мм с тем, чтобы компенсировать возможную его усадку. Ящик накрывают крышкой, кромки которой обмазывают огнеупорной глиной или смесью глины и речного песка, разведенных на воде до тестообразного состояния. После этого ящик помещают в печь. Смесь нагревают до 900 – 950 °С. Продолжительность выдержки при рабочей температуре зависит от требуемой толщины слоя и размеров ящика. Для получения пласта глубиной 0,7 - 1,5 мм выдержка составляет 6 – 15 ч. После цементации ящики охлаждают на воздухе до 400 – 500 °С и затем раскрывают.
В основе данного процесса лежат следующие химические превращения. В цементационном ящике имеется воздух, кислород которого при высокой температуре взаимодействует с углеродом карбюризатора, образуя СО. При этом угарный газ в присутствии железа разлагается по уравнению 2СО ® СО2 + Cат.
Углерод, выделяющийся в результате этой реакции, в момент его образования является атомарным и диффундирует в аустенит: Сат ® Fg ® Fg(С) - аустенит. Добавление углекислых солей сильно активизирует карбюризатор, обогащая атмосферу в цементационном ящике оксидом углерода (СО), вследствие протекания реакции ВаСО3 + С ® ВаО + 2СО.
Процесс твердого науглероживания имеет ряд недостатков: большое время (много вспомогательных операций), трудно поддается автоматизации и контролю; требуется большое количество обслуживающего персонала; оборудование очень громоздкое.
Наиболее распространенным способом является газовое науглероживание, имеющее ряд преимуществ. В ходе него можно точно получить заданную концентрацию углерода в слое; сокращается длительность процесса, так как отпадает необходимость прогрева ящиков, наполненных малотеплопроводным карбюризатором; обеспечивается возможность полной механизации и автоматизации процессов и значительно упрощается последующая термическая обработка изделий. При нем детали нагревают в атмосфере углеродсодержащих газов. Для этого используют природные или искусственные газы. Метан - более активный карбюризатор.
Основной реакцией, обеспечивающей науглероживание при газовой цементации, является диссоциация оксида углерода, образующегося в процессе окисления углеводородных газов, и диффузия формирующегося атомарного углерода в аустенит по вышеуказанным реакциям.
Газовую цементацию часто выполняют в безмуфельных или муфельных печах непрерывного действия, а также в шахтных печах периодического действия. При проведении процесса в последних для науглероживания применяют керосин, синтин, спирты и т. д., каплями подаваемые в печь. Высокая термическая устойчивость и хорошая испаряемость жидких углеводородов позволяют в одном рабочем пространстве совместить получение газа и процесс цементации.
В печах непрерывного действия применяют эндотермическую контролируемую атмосферу, в которую добавляют до 5 % природного газа. Основное ее преимущество - возможность автоматически регулировать углеродный потенциал. Под ним понимают науглероживающую способность атмосферы, обеспечивающую определенную концентрацию углерода на поверхности цементованного слоя.
Для сокращения длительности процесса широко используют газовую цементацию, при которой углеродный потенциал эндотермической атмосферы вначале поддерживают высоким, обеспечивающим получение в поверхностной зоне стали 1,2 - 1,3 % С, а затем его снижают до 0,8 % С.
Процессы выполняют при 930 – 950 °С. При этом сталь имеет структуру аустенита, растворяющего до 2 % С. Глубина цементованного слоя зависит не только от температуры, но и времени выдержки при ней. Поскольку его размеры редко требуются более 1,0 - 1,5 мм, процесс осуществляют за 8 - 12 часов. Например, продолжительность цементации для получения слоя толщиной 0,7 - 1,5 мм при 930 °С в муфельных (безмуфельных) печах непрерывного действия составляет 6 – 12 ч, а в шахтных 3 – 10 ч. Повышение времени или температуры вызовет рост зерен аустенита и ухудшит свойства слоя.
После цементации изделия приобретают мелкозернистую структуру заэвтектоидной стали, состоящей из перлита и вторичного цементита. Однако непосредственно по окончании процесса науглероживания детали не получают требуемых свойств. Это достигается термической обработкой. В ходе последующей ТО можно исправить структуру и измельчить зерно сердцевины и цементованного слоя, неизбежно увеличивающихся во время длительной выдержки при высокой температуре цементации, получить большую твердость в науглероженном пласте и хорошие механические свойства сердцевины; устранить карбидную сетку в цементованном слое, которая может возникнуть при насыщении его углеродом до заэвтектоидной концентрации. В большинстве случаев применяют закалку выше точки Ас1 (для сердцевины) при 820 – 850 °С.
По окончании газовой цементации используют закалку без повторного нагрева, а непосредственно из печи после подстуживания изделий до 840 –860 °С. Такая обработка не исправляет структуры науглероженного слоя и сердцевины и не приводит к измельчению зерна. Поэтому она применима только к наследственно мелкозернистой стали. Для уменьшения деформации цементованных изделий используют ступенчатую закалку в горячем масле 160 - 180 °С.
Иногда термическая обработка состоит из двойной закалки и отпуска. Первую закалку (или нормализацию) с нагревом до 880 – 900 °С назначают для исправления структуры сердцевины. Кроме того, при нагреве в поверхностном слое в аустените растворяется цементитная сетка, которая при быстром охлаждении вновь не образуется. Вторую закалку проводят с разогревом до 760 – 780 °С для устранения перегрева цементованного слоя и придания ему высокой твердости. Недостаток такой термической обработки заключается в большом объеме технологического процесса, повышенном короблении, возникающем в изделиях сложной формы, и возможности окисления и обезуглероживания.
В результате термической обработки поверхностный слой приобретает структуру мартенсита или мартенсита с небольшим количеством остаточного аустенита и избыточных карбидов в виде глобул.
Заключительной операцией термической обработки цементованных изделий во всех случаях является низкий отпуск при 160 – 180 °С, переводящий мартенсит закалки в поверхностном слое в отпущенный мартенсит.
Твердость поверхностного слоя для углеродистой стали составляет HRC 60 - 64, а для легированной HRC 58 - 61; снижение твердости объясняется образованием повышенного количества остаточного аустенита.
Сердцевина деталей из углеродистой стали имеет структуру сорбита, а из легированных - бейнита или низкоуглеродистого мартенсита. Низкоуглеродистый мартенсит обеспечивает повышенную прочность и достаточную вязкость сердцевины. Твердость сердцевины обычно составляет HRC 30 - 40.
Цементация с последующей термической обработкой повышает предел выносливости стальных изделий и понижает чувствительность к концентраторам напряжений при условии непрерывной протяженности упрочненного слоя по всей поверхности детали. Дополнительно предел выносливости цементованных изделий может быть повышен дробеструйным наклепом или обкаткой роликами.
Азотированием называется ХТО, при которой поверхностный слой детали насыщается азотом. Процесс осуществляется в атмосфере аммиака, который при нагревании разлагается. При этом увеличиваются не только твердость и износостойкость, а также предел выносливости и коррозионная стойкость в таких средах, как воздух, вода, пар и т. д.
Азотирование широко применяется для зубчатых колес, цилиндров мощных двигателей, многих деталей станков и других изделий.
В зависимости от условий работы деталей различают две разновидности процесса: для повышения поверхностной твердости и износостойкости («твердостное») и для улучшения коррозионной стойкости (антикоррозионное).
Продолжительность процесса в обоих случаях зависит от требуемой толщины азотированного слоя. Чем выше температура насыщения, тем ниже твердость и больше глубина азотированного пласта. Снижение твердости насыщаемого слоя связано с коагуляцией частиц нитридов легирующих элементов.
В первом случае детали насыщают азотом при 500 – 520 °С, процесс продолжается от 24 до 90 ч (скорость составляет около 0,01 мм/ч). Содержание азота в поверхностном слое достигает 10 – 12 %, толщина пласта - порядка 0,3 - 0,6 мм, твердость доходит до 1000 - 1200 единиц. Для ускорения процесса его проводят двухступенчато: вначале при 500 – 520 °С, а затем при 560 – 600 °С. Последующее охлаждение осуществляют вместе с печью в потоке аммиака.
Во втором случае азотирование проводят при 650 – 700 °С. Скорость диффузии увеличивается, продолжительность процесса сокращается до нескольких часов. На поверхности изделий образуется слой толщиной 0,01 - 0,03 мм, который обладает высокой коррозионной стойкостью. Для сокращения длительности процесса применяют азотирование в плазме тлеющего разряда.
Механизм процесса в обоих способах описывается следующими превращениями (1.1 и 1.2), включающими диссоциацию аммиака и поглощение атомарного азота железом.
2NH3 ® ЗН2 + 2Nат (1.1)
Nат ® Fea ® Fea(N) ® g'(Fe4N) ® e(Fe2-3N) (1.2).
Азотированный слой на железе состоит из нитридной зоны, представляющей собой смесь твердых растворов на основе нитридов железа Fe2-3N (e, 8,0 - 11,2 % N2) и Fe4N (g’, 5,60 - 5,95 % N2), и подслоя азотистого феррита (a), в котором при охлаждении выделяется нитрид железа Fe4N. При азотировании выше 600 °С между нитридным слоем и a-фазой образуется пласт азотистого аустенита (g).
Насыщению азотом подвергают среднеуглеродистые легированные стали, содержащие хром (Сг), молибден (Мо), ванадий (V), вольфрам (W) и алюминий (А1) и приобретающие особо высокую твердость и износостойкость. При этом образуются нитриды Сг2N, Mo2N, VN и др., которые, выделяясь в a-фазе (азотистом феррите) в дисперсном виде, препятствуют движению дислокаций и тем самым повышают твердость азотированного слоя. Наиболее сильно это делают нитриды ванадия, хрома, молибдена, а также алюминий, который растворяется в g'-фазе.
Если главными требованиями, предъявляемыми к азотированному слою, является высокая твердость на поверхности до HV 1200 и износостойкость, то применяют сталь 38Х2МЮА (0,35 - 0,42 % С; 1,35 - 1,65 % Сг; 0,70 - 1,10 % А1 и 0,15 - 0,25 % Мо). Молибден устраняет отпускную хрупкость в сплаве. В настоящее время для азотирования широко используют и другие конструкционные легированные стали.
В процессе насыщения азотом немного изменяются размеры изделия из-за увеличения объема поверхностного слоя. Деформация возрастает при повышении температуры азотирования и увеличении трещины пласта.
В последние годы получило распространение азотирование при 570 °С в атмосфере, содержащей 50 % объемн. эндогаза и 50 % NH3 или 50 % СН4 н 50 % NH3, а также в расплавленных солях (55 % NH2CO + 45 % Na2CO3), через которые пропускается сухой воздух (соли расплавляют в титановых тиглях). В результате такой обработки на поверхности образуется тонкий слой карбонитрида Fe2-3 (N, С), обладающий высокой твердостью (HV 600 - 1200) и износостойкостью. Такая обработка повышает предел выносливости.
Азотирование – завершающая операция при изготовлении деталей. Они подвергаются ей после окончательной механической и термической обработок – закалки с высоким отпуском. После этого в изделиях формируется структура сорбита, которая сохранится в его сердцевине и после насыщения и обеспечит ему повышенную прочность и вязкость. Такие детали имеют серый цвет.
Сравнивая цементацию и азотирование, можно отметить следующее: продолжительность первого вида обработки меньше; упрочненный слой получается более глубоким и допускает большие удельные давления при эксплуатации; твердость науглероженного слоя в 1,5 - 2,0 раза меньше и сохраняется при нагреве только до 180 – 125 °С, в то время как азотированный удерживает твердость до 600 – 650 °С.
Нитроцементацией называют процесс диффузионного насыщения поверхностного слоя стали одновременно углеродом и азотом при 840 – 860 °С в газовой среде, состоящей из науглероживающего газа и аммиака. Продолжительность процесса 4 – 10 ч. Основное назначение нитроцементации - повышение твердости, износостойкости и предела выносливости стальных деталей.
Для нитроцементации легированных сталей рекомендуется использовать контролируемую эндотермическую атмосферу, к которой добавляют от 1,5 до 5,5 % объемн. необработанного природного газа и 1,0 - 3,5 % объемн. NH3.
После нитроцементации следует закалка непосредственно из печи, реже вслед за повторным нагревом, применяют и ступенчатую закалку. Далее за закалкой проводят отпуск при 160 – 180 °С.
При оптимальных условиях насыщения структура нитроцементованного слоя должна состоять из мелкокристаллического мартенсита, небольшого количества мелких равномерно распределенных карбонитридов и 25 – 30 % остаточного аустенита.
Твердость пласта после закалки и низкого отпуска HRC 58 - 60, HV 5700 – 6900 МПа. Высокое содержание остаточного аустенита обеспечивает хорошую прирабатываемость.
Цианированием называют также совместное насыщение поверхности стали углеродом и азотом вследствие окисления расплавленных цианистых солей при нагревании до 820 – 960 °С.
Для получения слоя небольшой толщины (0,15 - 0,35 мм) процесс проводят при 820 – 860 °С в ваннах, содержащих 20 – 25 % цианистого натрия - NaCN, 25 – 50 % хлорида натрия - NaCI и 25 – 50 % кальцинированной соды – Na2CO3. Продолжительность насыщения определяется требуемой глубиной пласта и составляет 30 - 90 минут. Вслед за цианированием закалку выполняют непосредственно из цианистой ванны и дают низкотемпературный отпуск (180 – 200 °С). Твердость цианированного слоя после термической обработки - HRC 58 - 62; толщина пласта 0,15 - 0,30 мм. Этот вид цианирования применяют для мелких деталей.
Для получения слоя большой глубины (0,5 - 2,0 мм) цианирование проводят при 930 – 960 °С в ванне, содержащей 8 % NaCN, 82 % ВаС4 и 10 % NaCI. Зеркало ванны покрывают графитом для предупреждения больших потерь тепла и угара цианистых солей. Продолжительность выдержки изделий в ванне составляет 1,5 - 6,0 ч. При высоких температурах сталь с поверхности в большей степени насыщается углеродом (до 0,8 - 1,2 % С) и в меньшей степени - азотом (0,2 - 0,3 % N). После цианирования детали охлаждают на воздухе, а затем закаливают с нагревом в соляной ванне или печи и подвергают низкотемпературному отпуску. Структура цианированного слоя после закалки такая же, как цементованного. Глубокое цианирование применяют на некоторых заводах вместо цементации.
Диффузионной металлизацией называется ХТО, при которой поверхность стальных деталей насыщается различными металлами; алюминием, хромом, кремнием и др. После такой обработки повышаются жаро-, износо- и коррозионная стойкость.
Насыщение сталей металлами можно проводить при 900 – 1050 °С упаковкой изделий в соответствующие порошкообразные смеси (обычно ферросплавы и 0,5 – 5,0 % NH4C1), погружением их в расплавленный металл, если диффундирующий элемент имеет невысокую температуру плавления (например, цинк и алюминий), или насыщением из газовой среды. При газовом методе чаще применяют летучие хлористые соединения металлов (AlCl3, CrCl3, SiCl4 и т. д.), образующиеся при воздействии хлора (или хлористого водорода) на металлы или их сплавы (ферросплавы) с железом при высоких температурах. Хлориды взаимодействуют с железом, и выделяющийся в атомарном состоянии металл диффундирует в сталь. Насыщение металлами (например, хромом) проводят и путем испарения диффундирующего элемента в вакууме. Продолжительность процесса обычно 6 – 12 ч.
Алитирование-насыщение поверхности изделия алюминием. Оно осуществляется для стальных деталей с 0,1 - 0,2 %-ным содержанием углерода с целью повышения их окалиностойкости. Алитированный слой при этом имеет глубину 0,3 - 0,8 мм и обладает хорошим сопротивлением коррозии в некоторых средах. Он представляет собой твердый раствор алюминия в a-железе. Концентрация Al в поверхностной его части составляет около 40 %. Детали приобретают высокую жаростойкость, они могут работать при температуре до 1150 °С за счет образования на их поверхности плотной пленки из оксида алюминия Al2O3. Алитированию подвергают детали газогенераторных машин, разливочных ковшей, клапаны, чехлы термопар и другие изделия, работающие при высоких температурах.
Хромирование, т. е. насыщение поверхности стальных изделий хромом, обеспечивает повышенную устойчивость против газовой коррозии (окалиностойкость) до 800 °С, высокую коррозионную стойкость в таких средах, как пресная и морская вода, азотная кислота. У средне- и высокоуглеродистых сталей оно повышает твердость (до НV1600 - 1800) и износостойкость. Ему подвергают детали, изготовленные из сталей с самым различным содержанием углерода. Диффузионный слой, получаемый при хромировании технического железа, состоит из раствора хрома в a-железе. В процессе насыщения стали хромом пласт состоит из карбидов следующих составов (Cr,Fe)7C, (Cr,Fе)23С6. Твердость хромированного слоя составляет НV 250 - 300, а самого сплава НV 1200 - 1300. Глубина пласта не превышает 0,10 - 0,20 мм. Хромированию подвергают детали паросилового оборудования, пароводяной арматуры, клапанов, вентилей, патрубков, а также изделий, работающих на износ в агрессивных средах. Разработана технология глубокого вакуумного насыщения листовой низкоуглеродистой стали. Вакуумному хромированию на металлургических заводах подвергают также заготовки с последующей прокаткой их на листы и трубы.
Цинкование, - насыщение поверхностного слоя цинком для повышения коррозионной стойкости стали в атмосфере, пресной воде, бензине и некоторых других средах. Слой состоит из химических соединений FeZn7, FeZn3, к сердцевине прилегает a-фаза (твердый раствор цинка в a-железе). На металлургических заводах цинкованию подвергают тонкие листы, трубы, проволоку и готовые изделия (втулки, фитинги и т. д.).
Силицирование -насыщение поверхности деталей кремнием. Его проводят главным образом в газовой среде. Силицированный слой представляет собой твердый раствор кремния в a-железе. Концентрация Si здесь достигает 14 %. Силицирование повышает жаростойкость до 800 – 850 °С, слой хорошо сопротивляется истиранию и коррозионностоек даже в таких средах, как морская вода и азотной, серной и соляной кислотах, обладает повышенной пористостью. Насыщению кремнием подвергают детали, применяемые в оборудовании химической, бумажной и нефтяной промышленности (валики насосов, трубопроводы, арматура, гайки, болты и т. д.).
Борирование, т. е. насыщение поверхностного слоя бором, создает высокую твердость (НV 1800 - 2000), износо- и теплостойкость, а также устойчивость против коррозии в различных средах. Его чаще применяют для изделий из среднеуглеродистой стали. Получаемый слой на поверхности состоит из борида FeB, а ниже из – Fe2B и a-твердого раствора. После насыщения детали подвергают закалке ТВЧ или изотермической для уменьшения напряжений в поверхностном слое. Борирование применяют для повышения износостойкости втулок грязевых нефтяных насосов, вытяжных, гибочных и формовочных штампов, деталей пресс-форм, машин для литья под давлением и др. Стойкость указанных деталей после борирования возрастает в 2 - 6 раз.
Дата добавления: 2015-09-21; просмотров: 7120;