Выбор типа мотор – р
|
| |||||
|
Выбор типа мотор-редуктора. В качестве приводов могут быть использованы мотор-редукторы типа ВОМ, ВДМ, МПО-1 и МПО-2 (рис 3.4, 3.5). Это агрегаты, в которых конструктивно объединены электродвигатель и редуктор. Исходными данными для выбора мотор-редуктора служат требуемая мощность мешалки Рм и частота ее вращения nм. По табл. 27 выбирают типоразмер мотор-редуктора по условию Рдв ³ Ртр , nТ = nм, где Рдв – мощность электродвигателя; nТ - частота вращения выходного (тихоходного) вала мотор-редуктора. Требуемую мощность электродвигателя Ртр определяют по условию
,
где Р м - мощность на валу мешалки, кВт; h1 - КПД подшипников, в которых установлен вал (в соответствии с конструктивной схемой подшипникового узла); h2- КПД механической передачи (редуктора); h3 – КПД, учитывающий потери мощности в уплотнении; h4 - КПД, учитывающий потери в муфте. Значения КПД элементов привода принимают по табл. 28.
.
|
|
|
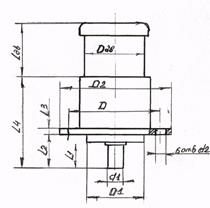
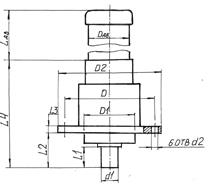
|
|
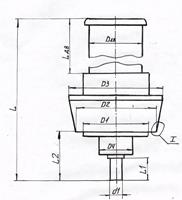
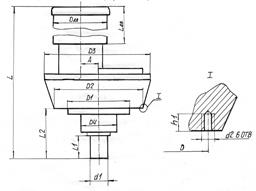
![]() |
В соответствии с выбранным типоразмером мотор-редуктора в табл. 29 - 37 приведены технические данные и основные размеры редукторов и комплектующих электродвигателей.
Выбор типа муфты. Для соединения вала мешалки с валом мотор-редуктора используют продольно-разъёмную, упругую втулочно-пальцевую или зубчатую муфты. С помощью продольно-разъёмной и зубчатой муфт возможно соединение валов одинакового диаметра, а с помощью упругой втулочно-пальцевой муфты - соединение валов разных диаметров. Тип муфты определяется конструктивной схемой опорного узла вала.
Продольно-разъёмные муфты (рис 3.6, табл.38) изготовляют для диаметров валов от 30 до 125 мм. Корпус с продольным разъёмом состоит из двух полумуфт. На наружные поверхности полумуфты надевают кольца, которые стягивают шпильками и гайками. За счёт конусности наружных поверхностей полумуфты кольцами прижимаются к соединяемым валам. Концы валов обрабатывают под фиксирующее кольцо, состоящее из двух половин, скрепляемых пружинами.
|
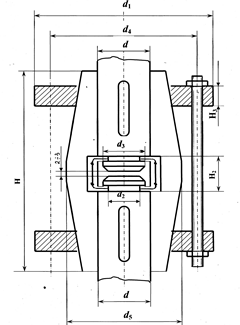
Зубчатая муфта (рис.3.7, табл. 39) состоит из двух втулок 1 с наружными зубьями, закрепленных на концах валов и охватывающих обоймы 2 с внутренними зубьями.
|
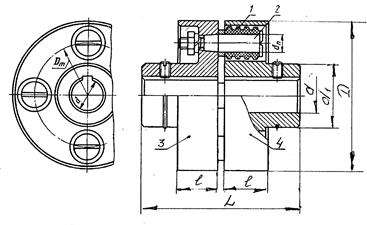
Втулочно-пальцевая муфта (рис.3.8, табл.40) включает в себя две полумуфты 3 и 4, насаживаемые на концы валов. Полумуфты соединены между собой пальцами 2 с надетыми па них резиновыми втулками 1.
Размеры муфты подбирают по диаметру вала мотор- редуктора d , и расчётному моменту Тр следующим образом:
1) Определяют угловую скорость вращения вала:
с-1 ,
где n - частота вращения мешалки.
2) Вычисляют вращающий момент на валу:
н×м ,
где Р - мощность на валу мешалки кВт;
3) Определяют величину расчётного момента:
Тр = k×Т,
где k - коэффициент режима работы, учитывающий условия эксплуатации ( k,= 1.1 - 1.2 для турбинных и трёхлопастных мешалок; k=1.2 - 1.5 - для рамных и лопастных мешалок);
4) по табл. 38 - 40 выбирают размеры соответствующей муфты.
Выбор стойки и опоры. Стойка имеет вид усечённого конуса, выполняемого из чугуна, с тремя опорными поверхностями (рис 3.9) . На верхней опорной поверхности монтируют мотор– редуктор, для чего в этой поверхности предусмотрены сквозные отверстия. Средняя поверхность служит для установки подшипникового узла, нижняя опорная поверхность предназначена для соединения стойки с опорой (бобышкой) 7 (см. рис.3.1, 3.2). Для удобства монтажа и демонтажа мотор-редуктора под опорной поверхностью предусмотрены окна размером 50x70 мм. Опора
(рис. 3.10) представляет собой бобышку с центральным отверстием размером d для вала и двумя рядами периферийных отверстий с резьбой для крепления стойки и уплотнения. Для установки опоры на эллиптических крышках путём сварки предусмотрено кольцо.
![]() |
Опоры, устанавливаемые на плоских крышках, таких колец не имеют. Их приваривают непосредственно к крышке аппарата. Размеры стоек приведены в табл. 41. Следует отметить, что высота стоек Н принимается конструктивно при выполнении этапа 5. В табл. 41 указана ее минимальная высота Н. Размеры опор приведены в табл. 42.
Выбор опор и стоек осуществляют после подбора мотор- редуктора и определения его габаритных и присоединительных размеров. По диаметру D расположения центров отверстий в опорном фланце
![]() |
(опорной поверхности) мотор–редуктора по табл. 41 выбирают стойку, у которой центры отверстий в верхней опорной поверхности 1 выполнены на том же диаметре D. Опору с помощью болтов (шпилек и гаек) соединяют со стойкой. Поэтому диаметр центров отверстий,выполненных на нижней опорной поверхности стойки 3, должен быть согласован с диаметром
центров отверстий с резьбой в опоре (рис 3.9, 3.10).
|
Разработка эскизного варианта завершается выполнением на миллиметровке формата А1 чертежа общего вида аппарата в масштабе 1:10 или 1:15 с допускаемыми упрощениями (по ГОСТ 2.109-73) . На этом чертеже рекомендуют изобразить главный вид аппарата с приводом и вид сверху. Положение ступицы мешалки на валу определяются расстоянием hм от середины ступицы до днища аппарата. Конструкции мешалок и способы их крепления на валу приведены на рис. 1 – 6 прил.2. Размеры мешалок принимают по табл. 43 – 46 прил.1.
Для корпусов с эллиптическим днищем турбинную и трёхлопастную мешалки располагают на расстоянии hм = dм,рамную и лопастную – на расстоянии hм = 0,1dм .
Для корпусов с коническим днищем трёхлопастную, лопастную и турбинную мешалки располагают на расстоянии hм, равном высоте конической части днища hм = HD , рамную – на расстоянии hм = 0,1dм.
3.3 Последовательность проектирования и расчёта перемешивающего устройства
Проектирование и расчет перемешивающего устройства осуществляют в следующей последовательности:
1) выполняют проектный расчет и конструирование вала и
подшипникового узла;
2) разрабатывают эскизную компоновку перемешивающего
устройства;
3) выполняют проверочный расчет вала;
4) проверяют пригодность подшипников, уточняют конструкцию подшипниковых узлов.
3.4. Проектный расчёт и конструирование вала и подшипникового узла
Проектный расчёт вала. Расчёт выполняется по напряжениям кручения. Целью расчёта является определение наименьшего диаметра вала. Исходными данными являются мощность на валу Р (кВт) и частота вращения мешалки n (об/мин).
Рассчитывают угловую скорость вала:
, сек-1 . (3.1)
Вычисляют вращающий момент
, Н×м . (3.2)
Определяют наименьший диаметр вала:
, мм , (3.3)
где =25 … 40 Мпа.
Конструирование вала и подшипникового узла. Конструкция вала определяется деталями, которые на нём крепятся, конструктивным оформлением подшипниковых узлов и способом соединения вала перемешивающего устройства с валом редуктора.
Для соединения валов применяют разные типы муфт. Соединение вала редуктора с валом перемешивающего устройства продольно-разъёмной муфтой считают жёстким. Втулочно-пальцевая и зубчатая муфты образуют подвижное соединение валов.
Подшипниковый узел (рис 3.11 – 3.12) состоит из корпуса 1, внутри которого установлен один радиальный или два радиально-упорных подшипника качения 2. Между подшипниками установлена распорная втулка 3(рис.3.12). Для фиксации вала в осевом направлении предусмотрена круглая шлицевая гайка 4, которая предохраняется от самоотвинчивания стопорной многолапчатой шайбой 5. Корпус закрыт крышками 6, в сквозных отверстиях которых установлены манжетные уплотнения. 7.
|


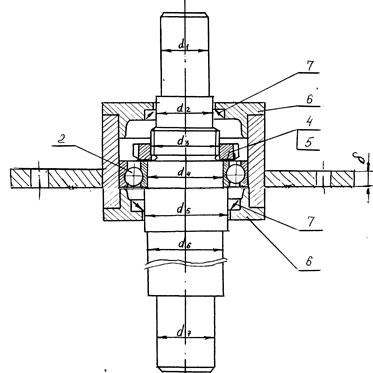
|
Рассмотрим порядок конструирования консольного вертикального вала с двумя подшипниками качения (рис. 3.12).
1. Верхний конец вала соединяют с валом редуктора стандартной муфтой. Если соединение валов подвижное (с помощью зубчатой или упругой втулочно-пальцевой муфты), то диаметр d1=(0,8...1)d. Длину этого участка вала принимают равной l1»(1...1,5)d1 и уточняют по размерам муфты. В случае жесткого соединения валов продольно-разъёмной муфтой, его диаметр d1 рекомендуют принимать равным диаметру d выходного (тихоходного) вала редуктора.
2. Диаметр вала d2 под уплотнение (в крышке подшипникового узла) берут равным d1+(4...7).мм и округляют до ближайшего стандартного из ряда: 30,32,34,36,38,40,42,45,48,50, 53,56,60,67,67.75.80,85,90,95.100, 105, 110,120. Длина этого участка l2 определяется конструктивно с учётом размеров верхней крышки:
l2 »(в+s) + 10 мм, где в - ширина манжеты, s = 5 - 8 мм - толщина крышки в месте установки манжеты. Размеры манжетных уплотнений выбирают по диаметру вала d2 (табл. 47). Остальные размеры крышки – см. стр.40.
3. Диаметр участка с резьбой под шлицевую гайку d3 = d2 + (2…4) мм должен быть согласован с размером резьбы в гайке (табл.17, прил.1). Длина данного участка l3»(Н+S) + 5мм. Толщина шайбы S – табл.2.18, прил.1.
4. Следующий участок вала предназначен для посадки подшипника. Его диаметр d4 > d3 должен быть согласован с диаметром отверстия внутреннего кольца подшипника. На стадии эскизного проекта первоначально принимают шариковые радиально-упорные подшипники лёгкой серии (рис 3.13, табл. 49, прил.1). Длина этого участка вала l4 » В + 5, где В - ширина подшипника.
5. Между подшипниками качения устанавливают распорную втулку, внутренний диаметр которой равен диаметру d4. Наружный диаметр втулки dвт = d4 + (6…8) мм. Длина lвт»2D, где D - диаметр наружного кольца подшипника (табл.49, прил.1). Для удобства монтажа диаметр вала под втулкой принимают на 4 - 5 ммменьше значения d4.
![]() | |||
|
6. Для упора нижнего подшипника диаметр вала увеличивают: d5 » dвт. Длина l5 этого участка вала принимается конструктивно, аналогично l2, с учётом размеров нижней крышки подшипникового узла l5»(в+s) + 10 мм. Размеры манжеты выбирают по табл. 47 прил.1 в зависимости от диаметра d5. Размеры крышки - см. пункт 2.
|
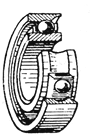
|
|
|
|
7. Диаметр d6 следующего участка вала необходимо согласовать с диаметром отверстия в сальниковом или торцевом уплотнении (табл. 51,52 прил.1).
8. Участок вала d7 в месте посадки мешалки принимают равным диаметру отверстия в ступице мешалки dст (табл.43 – 46 прил.1, рис.5 – 6 прил.2).
|
При конструировании однопролетного вала (см. рис.3.1 б,
3.2 б) диаметр посадочного участка вала должен соответствовать размеру d1 в концевой опоре скольжения (рис 3.17, табл. 53 прил.1).
Конструирование корпуса и крышек подшипникового узла. После определения геометрических размеров ступеней вала определяют размеры деталей, входящих в подшипниковый узел
(рис 3.11 и 3.12).
Толщину стенки корпуса подшипникового узла s принимают равной 10-12 мм. Диаметр резьбы винтов dв для крепления крышек к корпусу и их число z назначают в зависимости от наружного диаметра подшипника D:
D, мм | 80 - 90 | 100 - 140 | 150 - 200 |
dв ,мм | М8 | М10 | М12 |
z |
|
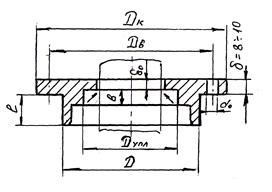
Размеры винтов приведены в табл. 15 прил.1. Наружный диаметр крышки Dк »D + 4dв. Диаметр центров отверстий под винты Dв »D + 2dв. Толщина крышки в месте установки винтов d = 8¸10 мм. Толщина крышки в месте установки манжеты d0 = 5¸8 мм. Остальные размеры крышек (рис.3.14) зависят от размеров манжеты, размер l принимается конструктивно.
В конструкции, представленной на рис.3.12, для удобства монтажа подшипников часть внутренней поверхности корпуса (между торцами подшипников) выполняют на 2 мм больше, чем диаметр подшипника D, длина этой части корпуса равна длине распорной втулки. К корпусу приварен фланец толщиной d = 10 мм с отверстиями d=1,1 dв для крепления подшипникового узла в стойке привода.
3.5. Разработка эскизного проекта перемешивающего устройства.
Эскизную компоновку выполняют масштабе 1:1 на миллиметровой бумаге формата А2 или А1. Для получения представления о конструкции и размерах деталей перемешивающего устройства достаточно одной проекции.
Последовательность выполнения эскизного проекта:
1. Провести осевую линию в середине короткой стороны листа.
2. В верхней части листа вычертить верхнюю опорную поверхность стойки. Определить положение верхнего торца выбранной муфты. Для этого от верхней опорной поверхности стойки отложить вниз отрезок L2 – L1 (см. размеры выбранного мотор–редуктора).
3. От полученной линии отложить вниз отрезок, равный длине выбранной муфты L (Н). Последняя линия будет являться торцом участка вала d2.
4. Отступив вниз примерно на 10 мм, провести линию, определяющую положение верхней крышки подшипникового узла. Следующая линия определяет толщину крышки в месте установки манжетного уплотнения, и вычертить «карман» для манжеты по размерам, приведенным в табл.47 прил.1.
5. Между внутренней поверхностью крышки и торцом участка вала диаметром d3 оставить примерно 10 мм.
6. Вычертить контуры круглой шлицевой гайки и стопорной шайбы.
7. Вычертить по контуру верхний подшипник. Отложить от его нижнего торца расстояние, равное длине распорной втулки lвт, и вычертить контуры нижнего подшипника. Для схемы с одним подшипником качения в стойке перейти к пункту 8.
8. От торца нижнего подшипника отложить примерно 5-7 мм. Этим определяется положение внутренний поверхности нижней крышки.
9. Вычертить контуры нижней крышки и участка вала диаметром d5.
10. От наружной поверхности нижней крышки отложить примерно 20 мм. Этим определяется положение сальникового или торцового уплотнения.
11. Вычертить контуры выбранного уплотнения, крышки (дочертить) и корпуса подшипникового узла. Уплотнение и стойку закрепить на опоре привода.
3.6. Проверочный расчёт вала
Основными критериями работоспособности валов перемешивающих устройств являются виброустойчивостъ и прочность.
Прежде чем приступить к расчёту вала, необходимо выбрать расчётную схему и определить длину расчётных участков вала.
Выбор расчётной схемы. Каждому конструктивному решению крепления вала соответствует своя расчетная схема.
1. Жесткое соединение валов мотор-редуктора и мешалки (продольно-разъёмной муфтой). Если при этом вал опирается на один радиальный подшипник качения, установленный в стойке аппарата (рис.3.1 а), то такому конструктивному решению соответствует расчётная схема 1 (рис.7 прил.2). Если опорой вала служит подшипник скольжения, установленный на днище аппарата
(рис.3.1 б), данному конструктивному решению соответствует расчётная схема 2 (рис.8 прил.2).
2. Подвижное соединение валов (втулочно-пальцевой или зубчатой муфтой). Если опорами вала является два радиально-упорных подшипника качения (рис.3.2 а), такому решению соответствует расчётная схема 3 (рис.9 прил.2). Если верхней опорой является радиально-упорный подшипник качения, размещенный в стойке, а второй - подшипник скольжения, установленный на днище аппарата (рис.3.2 б), то данному решению соответствует расчетная схема 4 (рис10 прил.2).
Расчёт на виброустойчивость. Расчет осуществляют в следующей последовательности:
1. Определить массу единицы длины вала:
кг × м, (3.1)
где r =7,85 ×10 3 кг/м3 - плотность материала вала; d (d6) - диаметр вала в месте уплотнения, м.
2. Вычислить момент инерции поперечного сечения вала:
. м4 . (3.2)
3 Определить значение коэффициентов:
,
, (3.3)
где Мм - масса мешалки, кг (табл.43 – 46 прил.1), l1 , L – значения длин соответствующих участков вала, м (по расчетной схеме и компоновке или чертежу).
4. В соответствии с выбранной расчётной схемой определить коэффициент a (рис. 7 – 10 прил.2).
5. Определить критическую скорость вала :
, с -1 , (3.4)
где Е = 2 • 1011 - модуль продольной упругости вала.
Проверить выполнение условия
. (3.5)
Если условие (3.5) не выполняется, то необходимо увеличить диаметр вала d6 в месте установки уплотнения (см. табл. 51 – 52 прил.1) и повторить расчет. При этом надо учесть, что эта мера приведёт к изменению размеров всех ступеней вала и деталей, расположенных на нём.
Расчёт на прочность. Расчёт предусматривает определение эквивалентных напряжений вала в опасных сечениях (в местах с наибольшим изгибающим моментом). Выбор таких сечений выполняют после построения эпюр изгибающих и крутящих моментов.
Изгиб вала происходит под действием инерционных сил, возникающих вследствие несбалансированности масс мешалки и вала.
Последовательность расчёта:
1. Определить эксцентриситет центра массы перемешивающего устройства:
е = 0.5 × 10-3 + 0,03× Dмеш , (3.6)
где Dмеш - диаметр мешалки, м.
2. Определить значение приведённой массы мешалки и вала
, (3.7)
где q - коэффициент приведения распределённой массы вала к сосредоточенной массе мешалки.
Для 1-й расчётной схемы .
Для 2-й расчётной схемы .
где .
Для З-й расчётной схемы .
Для 4-й расчётной схемы .
3. Определить радиус вращения центра тяжести приведенной массы мешалки и вала:
. (3.7)
4. Определить центробежную силу:
, (3.8)
где Мпр - приведённая масса мешалки и вала, кг; r - радиус вращения центра тяжести приведённой массы, м.
5. В соответствии с выбранной расчетной схемой вала определить радиальные реакции в опорах.
Для 1-й схемы ,
.
Для 2-й схемы ,
.
Для З-й схемы ,
.
Для 4-й схемы ,
.
6. Построить эпюры изгибающих и крутящих моментов и определить величины изгибающих моментов в опасном сечении вала. Для 1-й расчётной схемы опасным является сечение под подшипником, для 2-й и 4-й - сечение в месте посадки мешалки, для 3-й схемы – сечение под нижним подшипником.
7. Определить напряжение изгиба и напряжение кручения
в опасном сечении:
, н/мм2 ; (3.9)
, н/мм2 . (3.10)
8. Рассчитать эквивалентное напряжение и проверить выполнение условия
. (3.11)
Значение допускаемого напряжения рассчитывают по формуле
, (3.12)
где - предел выносливости материала вала
. Значение предела прочности s в берут из табл. 54 прил.1. S min - минимальный запас прочности вала (ориентировочно S min= 2); Кs - коэффициент концентрации напряжений, который для 1-й и 3-й схем: Кs= 1,2 - 1,5 (опасное сечении под подшипником), а для 2-й и 4-й схем: Кs = 1,5 - 2(опасное сечение под мешалкой ослаблено шпоночным пазом).
3.7.Проверочный расчёт шпонок
Призматические шпонки проверяют на смятие. Проверке подлежат две шпонки - в месте посадки полумуфты и в месте установки мешалки.
Условие прочности:
, (3.13)
где d - диаметр вала в месте установки шпонки; 1р = (1 – в) - рабочая длина шпонки со скругленными торцами в мм (1-полная длина шпонки); в,h,t - стандартные размеры (табл.55 прил.1, рис. 3.15); [sсм] = 80 - 150 н/мм2 - допускаемое напряжение на смятие.
|
3.8.Проверка пригодности подшипников
Пригодность подшипников качения определяется сопоставлением расчётной динамической грузоподъемности Ср с базовой (табличной ) С.
Расчёт динамической грузоподъёмности производится по формуле
, (3.14)
где Lh срок службы (ресурс) узла; Lh = 10 • 103 ¸ 20 • 103 ч; п - число оборотов вала в минуту; РЕ - эквивалентная динамическая нагрузка ;
m =3 (для шарикоподшипников).
Определение сил, нагружающих подшипники. Радиальные нагрузки Fr на подшипники равны радиальным реакциям RA , RB (см. расчет вала на прочность).
Осевые нагрузки. При установке вала в шариковых радиальных подшипниках осевая сила Fa, нагружающая подшипник, равна внешней осевой силе F A, действующей на вал:
, (3.15)
где Р - давление в аппарате; G - вес вала и мешалки; dрас - расчётный диаметр вала в уплотнении, установленном на крышке аппарата (d6); dрас =d+5 мм.
При размещении вала в радиально-упорных подшипниках осевые силы Fa, нагружающие подшипники, находят с учётом осевых составляющих S от действия радиальных сил Fr: для шарикоподшипников S = e ×Fr ; для роликоподшипников – S = 0,83 e ×Fr ; где Fr - реакция наиболее нагруженной опоры (RA или RВ); е - коэффициент осевого нагружения подшипника (табл.50).
Дата добавления: 2015-08-01; просмотров: 3541;