АЗОТИРОВ4НПЕ
Азотированием называют процесс диффузионного насыщения поверхностного слоя стали азотом при нагреве ее в аммиаке. Азотирование очень сильно повышает твердость поверхностного слоя, его износостойкость, предел выносливости и сопротивление коррозии в таких средах, как атмосфера, вода, пар и т.д. Твердость азотированного слоя заметно выше, чем цементованной стали, и сохраняется при нагреве до высоких температур (550 – 600 °С), тогда как твердость цементованного слоя сохраняется только до 200 – 225°С.
Механизм образования азотированного слоя. В сплавах железа с азотом образуются следующие фазы (рис. 1): твердый раствор азота в α-железе (α-фаза); γ'-фаза – твердый раствор на основе нитрида железа Fe4N (5,7 – 6,1 % N); ε-фаза – твердый раствор на базе нитрида железа Fe3N (8 –
11,2 % N). В сплавах с 11,35% N при 450 0С возможно образование ζ-фазы Fe2N.
При температуре выше 591 0С существует γ-фаза, которая представляет собой твердый раствор азота в γ-железе.
|
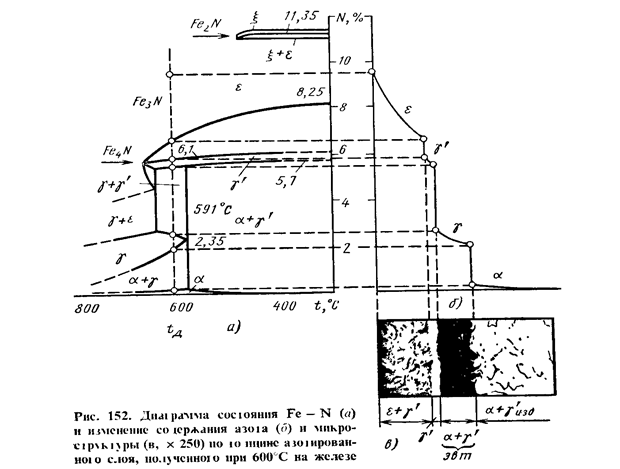
Азотирование проводят в атмосфере аммиака, который при нагреве диссоциирует по уравнению 2NН3 → 2N + 6Н.
Образовавшийся атомарный азот диффундирует в железо. Если выполнять азотирование при температуре ниже 591°С, то в начальный момент насыщения на поверхности стали образуется α-фаза (рис. 1,а). По достижении предела насыщения α-фазы начинается образование следующей фазы, стабильной при данной температуре, а именно γ'-фазы. При дальнейшем насыщении азотом образуется ε-фаза. Следовательно, в результате диффузии в азотированном слое располагаются в поверхностной зоне наиболее богатая азотом ε-фаза, несколько ниже γ'- и α-фаза.
С понижением температуры ε- и α-фазы в соответствии с диаграммой состояния (см. рис. 1, в) распадаются, выделяя избыточную γ'-фазу. В связи с этим после медленного охлаждения фазы в диффузионном слое можно расположить в следующем порядке от поверхности к сердцевине: ε + γ'п → γ' → α + γ' → α → сердцевина (с исходной структурой).
При выполнении азотирования выше 591°С, например при tд (рис. 1), сначала возникает α-фаза, затем по достижении ее предела насыщения образуется γ-фаза, после насыщения которой на поверхности появляется γ'-фаза, и, наконец, ε-фаза. Таким образом, при температуре диффузии азотированный слой состоит из следующих фаз (от поверхности к сердцевине): ε → γ' → γ → α. При медленном охлаждении ε- и α-фазы распадаются и выделяют избыточную γ'-фазу (Fe4N), а γ-фаза претерпевает превращение, распадаясь на структуру α + γ'. Тогда при 20°С азотированный слой будет состоять из ε + γ' → γ' → α + γ' → α + γ'п → α (см. рис. 1).
Переход от одной фазы к другой сопровождается резким перепадом концентрации азота, так как двухфазные слои (ε + γ' или α + γ') при температуре насыщения железа азотом существовать не могут (см. рис. 1).
При насыщении легированных сталей при температуре диффузии могут образоваться многофазные слои.
Стали для азотирования. Твердость слоя, получаемого при азотировании железа, невелика, поэтому азотированию подвергают среднеуглеродистые легированные стали, которые приобретают особо высокую твердость и износостойкость.
Если главными требованиями, предъявляемыми к азотированному слою, являются высокие твердость и износостойкость, то применяют сталь 38Х2МЮА, содержащую 0,35-0,42%С; 1,35-1,65% Сr; 0,7-1,10% Аl и 0,15-0,25% Мо. Одновременное присутствие алюминия, хрома и молибдена позволяет повысить твердость азотированного слоя до НV 1200. Молибден, кроме того, устраняет отпускную хрупкость, которая может возникнуть при медленном охлаждении от температуры азотирования. Легирующие элементы, повышая твердость, одновременно уменьшают, при прочих равных условиях, толщину слоя. Для повышения коррозионной стойкости можно азотировать и углеродистые стали.
Износостойкость азотированной стали выше, чем цементованной и закаленной.
Технология процесса азотирования. Технологический процесс предусматривает несколько операций, приведенных ниже.
1. Предварительная термическая обработка заготовки. Эта операция состоит из закалки и высокого отпуска стали для получения повышенной прочности и вязкости в сердцевине изделия.
Закалку стали 38Х2МЮА выполняют с нагревом до 930-950°С с охлаждением в воде или в масле. Отпуск проводят при высокой температуре 600-675°С, превышающей максимальную температуру последующего азотирования и обеспечивающей получение твердости, при которой сталь можно обрабатывать резанием.
2. Механическая обработка деталей, а гакже шлифование, которое придает окончательные размеры детали.
3. Защита участков, не подлежащих азотированию, нанесением тонкого слоя (0,01—0,015 мм) олова электролитическим методом или жидкого
стекла. Олово при температуре азотирования расплавляется на поверхности стали в виде тонкой не проницаемой для азота пленки.
4. Азотирование.
5. Окончательное шлифование или доводка изделия.
Азотирование тонкостенных изделий сложной конфигурации рекомендуется выполнять при 500 – 520°С. Длительность процесса зависит от требуемой толщины азотированного слоя. Чем выше температура азотирования, тем ниже твердость азотированного слоя и больше толщина слоя. Обычно при азотировании желательно иметь слой толщиной 0,3-0,6 мм. Процесс азотирования при 500 – 520°С в этом случае является продолжительным и составляет 24-60 ч.
В процессе насыщения азотом изменяются, но очень мало, размеры изделия вследствие увеличения объема поверхностного слоя. Деформация возрастает при повышении температуры азотирования и толщины слоя.
Для ускорения процесса азотирования нередко применяют двухступенчатый процесс: сначала азотирование проводят при 500 – 520°С, а затем при 540 – 560°С. При двухступенчатом процессе сокращается продолжительность процесса, при этом сохраняется высокая твердость азотированного слоя. Охлаждение после азотирования производят вместе с печью в потоке аммиака (до 200°С) во избежание окисления поверхности.
Дата добавления: 2015-02-16; просмотров: 1190;