Электрооборудование сварочных установок
Электросварочные установки являются специфичными электроприемниками электроэнергии. В соответствии с ПУЭ питание сварочной дуги не допускается от силовой, осветительной или контактной электрической сети.
Основное электрооборудование электросварочных установок включает источник питания (ИП), электроприводы перемещения тележек и подачи сварочной проволоки (при необходимости, у автоматов и полуавтоматов), коммутационную, защитную и управляющую аппаратуру, устройства для поджигания и стабилизации дуги. По технологии процесса различают следующие виды электросварки: дуговая, контактная и специальные.
В зависимости от технологии электросварки источники питания могут быть общепромышленные и специальные. Применяются следующие виды ИП: постоянного тока (электромашинные преобразователи, выпрямители и передвижные сварочные подстанции) и переменного тока (одно- и трехфазные трансформаторы 380 В). В зависимости от вида энергии и характера ее преобразования различают следующие типы источников питания: трансформатор, выпрямитель, генератор, преобразователь, агрегат и др. В настоящее время нашли широкое применение инверторные источники питания для самых различных видов электросварки.
Все оборудование для электросварки можно разделить на две большие группы по принципу работы: аппараты трансформаторного типа и инверторные аппараты. Строго говоря, трансформатор присутствует во всех аппаратах, однако в оборудовании трансформаторного типа преобразование энергии происходит на частоте питающей сети, в то время как в аппаратах инверторного типа преобразование происходит на частотах порядка 100 кГц. Традиционными характерными преимуществами трансформаторного оборудования являются: надежность, простота в использовании, сравнительная дешевизна.
Все трансформаторное оборудование можно разделить на две группы: простые (ВД301, ВД1201 и др., в том числе зарубежные трансформаторы фирм типа SekoUnistep и др.) и тиристорные аппараты (ВДУ506, УДГУ350 и др.). Надежность простых нерегулируемых трансформаторных аппаратов достигается благодаря простоте устройства. Аппарат состоит из трансформатора, выпрямителя и сглаживающего дросселя. Для регулирования сварочного тока используется ступенчатое переключение напряжений, а для смягчения жесткой вольтамперной характеристики используют балластное сопротивление. КПД установки с балластным сопротивлением не превышает 30%, что не дает эффективного производства.
Оборудование тиристорного типа позволяет изменять выходную характеристику без применения балластного сопротивления. Принципиальное отличие аппаратов такого типа от простых трансформаторных состоит в использовании управляемого тиристорного выпрямителя вместо неуправляемого.
В выпрямителе трансформатор выполняет функции понижения напряжения, а иногда еще формирования необходимой внешней характеристики и регулирования режима. На рис. 7.22 показана конструкция трехфазного трансформатора. На каждом из трех стержней магнитопровода 3 размещены по одной первичной 1 и одной вторичной 2 обмотке соответствующей фазы.
а б
в г
Рис. 7.22. Конструкция трехфазных трансформаторов с нормальным (а, б)
и увеличенным (в, г) рассеянием
Магнитопровод набирается из отдельных пластин, изолированных лаком для уменьшения вихревых токов (рис. 7.22, а). Находят применение витые ленточные магнитопроводы (рис.7.22, б), которые после навивки и скрепления лаком распиливают пополам, что облегчает сборку и ремонт трансформатора. Цилиндрические первичные и вторичные обмотки навиваются из алюминиевого изолированного провода, реже – из медного. Если вторичную обмотку концентрично разместить на первичной, то трансформатор имеет малое магнитное рассеяние (рис. 7.22 а, б) и формирует жесткую внешнюю характеристику. При размещении первичной и вторичной обмоток на значительном расстоянии друг от друга получают трансформатор с увеличенным рассеянием (рис. 7.22, в) и падающей внешней характеристикой. Магнитопроводы, показанные на рис. 7.22, а, б, в, называют несимметричными. Действительно, магнитное сопротивление на пути потока, создаваемого обмотками фазы В, меньше, чем для фаз А и С, поэтому ток в фазе В выше остальных, а в кривой выпрямленного тока появляется гармоническая составляющая с частотой 100 Гц, накладывающаяся на основную с частотой 300 Гц. Симметричный магнитопровод (рис. 7.22, г) имеет более сложное устройство, дороже и поэтому не нашел применение.
В качестве понижающего трансформатора в сварочных выпрямителях чаще всего используют трехфазные трансформаторы с нормальным или повышенным магнитным рассеянием, также трансформаторы с жесткой характеристикой (для электрошлаковой сварки). Особенно широкое распространение получили трансформаторы с подвижными катушками. Они просты по устройству, обладают высоким КПД, имеют небольшую массу. Такие трансформаторы имеют два диапазона сварочных токов, обеспечиваемых соответствующим соединением первичных и вторичных обмоток.
В конструкциях отечественных сварочных выпрямителей чаще используют селеновые или кремниевые силовые вентили (неуправляемые диоды, неполностью управляемые тиристоры и управляемые транзисторы) с принудительным воздушным охлаждением. В частности, сварочный выпрямитель типа ВД-306УЗ является источником питания постоянного тока с падающими внешними характеристиками. На базе управляемых вентилей (тиристоров и транзисторов) созданы выпрямители с промежуточным высокочастотным звеном – инвертором. Силовые транзисторы, благодаря уникальным возможностям регулирования, нашли широкое применение.
Инвертор – это устройство, преобразующее постоянное на-пряжение в высокочастотное переменное. В выпрямителе с инвертором используются амплитудное, частотное и широтное регулирование сварочного режима. Естественные внешние харак-теристики выпрямителя зависят от конструкции инвертора и трансформатора.
Оборудование инверторного типа зарекомендовало себе следующими характерными чертами: качество сварки, гибкость применения, компактность и легкость транспортировки, экономия электроэнергии [41]. Современное сварочное оборудование, построенное на базе инверторных источников, дает существенную экономию электроэнергии за счет высокого КПД и высокого коэффициента мощности. С появлением инверторных источников ранее применяемые источники питания называют конвециональ-ными, т.е. традиционными.
Входной выпрямительный блок V1 (рис. 7.23) преобразует переменное напряжение сети в постоянное, которое сглаживается с помощью низкочастотного фильтра L1, C1. Далее выпрямлен-ное напряжение преобразуется в однофазное переменное
высокой частоты с помощью инвертора на двух транзисторах VT1 и VT2. Далее напряжение понижается трансформатором T до
, выпрямляется блоком вентилей V2, проходит через фильтр L2, C2 и подается на дугу в виде сглаженного напряжения
.
Рис. 7.23. Выпрямитель с транзисторным инвертором
Процесс инвертирования. При подаче сигнала на базу тран-зистора VT1 отпирается его коллекторная цепь, и по первичной об-мотке трансформатора Т в интервале времени протекает ток в направлении, показанном тонкой линией. При снятии сигнала с базы этот ток прекращается. С некоторой задержкой отпирается транзистор VT2, при этом в интервале времени
ток по транс-форматору идет уже в другом направлении (показанно пункти-ром). Таким образом, по первичной обмотке трансформатора идет переменный ток. Длительность его периода Т и частота переменного тока f = 1/T зависят от частоты запуска транзисторов, определяемой частотой управления. Обычно частота устанавливается на уровне 1…100 кГц. Эта частота не зависит от сети, такой инвертор называют автономным. Если инвертор конструктивно объединяют с трансформатором Т, выпрямительным блоком V2 и фильтром L2-C2, то такое устройство называют конвертором, у него на выходе, как и на входе, постоянное напряжение, но меньшей величины.
Если на входе инвертора установлен мощный накопительный конденсатор С1, то напряжение инвентора имеет прямоуголь-ную форму (рис. 7.23, б). Такую конструкцию называют автоном-ным инвертом напряжения (АИН). И если на входе инвертора установить мощный дроссель L1, а обмотку трансформатора Т шунтировать конденсатором, то сглажен будет уже входной ток. Такой преобразователь называется автономным инвертором тока (АИТ). Нако-нец, возможна конструкция, в которой благодаря наличию после-довательно соединеных индуктивности и емкости образуется колебательный контур с синусоидальным током, она называется резонансным инвертором (АИР).
Сварочные свойства выпрямителей с инвертором лучше, чем у конвециональных источников, и объясняется это высоким быстродействием инвертора. Если у неинверторного однофазного выпрямителя длительность переходного процесса составляет не менее полупериода стандартного переменного тока, т.е. около 0,01 с, то у выпрямителя с инвертором быстродействие характеризуется значениями 0,0005 с и меньше.
Достоинство и недостатки выпрямителя с инвертором тесно связаны друг с другом. Энергия здесь претерпевает, по крайней мере, четыре ступени преобразования. Но тем не менее выпрями-тель такой экономичен. Сердечник высокочастотного трансфор-матора имеет малые массу и сечение. Поскольку масса связана с частотой соотношением , то обычно сердечник весит в десятки раз меньше, чем сердечник трансформатора на 50 Гц. Сам выпрямитель имеет следующие массэнергетические характеристики: 0,02…0,1 кГ на 1 А сварочного тока и 1…4 кГ на 1 кВт потребляемой мощности, т.е. в 5…15 раз меньше других выпрямителей. Главный недостаток выпрямителя с инвертором – чрезмерная сложность устройства.
Силовые элементы выпрямителей отличаются от конвецио-нальных малыми габаритами и массой, что связано с высокой частотой преобразования энергии. Миниатюризации не подверга-ются только входной выпримительный блок и его фильтр. Отмечается, что понижающий трансформатор дает самый большой выигрыш в массе (увеличение частоты с 50 Гц до 50 кГц приводит к снижению массы со 120 до 7 кг), пропорционально снижается масса сглаживающего дросселя.
Принципиальные отличия, предопределяющие возможности и свойства выпрямителей с инвертором, относятся к преобразова-нию высокого постоянного напряжения в низкое постоянное с промежуточным звеном высокой частоты, поэтому нужно разли-чить высокочастотные преобразователи (конверторы). Конверто-ры – это конструкция, состоящая из инвертора, трансформатора и выходного выпрямительного блока. В сварочных выпрямителях нашли применение конверторы однотактные с прямым и обрат-ным включением выходного тока, мостовые и полумостовые двухтактные, также все названные с резонансным инвертором.
При наличии в цехе большого количества постов сварки из-готовляют многопостовые выпрямительные системы на токи 630, 800, 1000, 1250, 1600, 2000, 3150, 4000 и 5000 А. Система имеет общий источник, шинопровод и постовые устройства (рис. 7.24). Распространены простые системы (рис. 7.24, а), в ней исполь-зуется многопостовой выпрямитель, состоящий из трансформатора Т и выпрямительного блока V. Шинопровод выполняется общим для всего цеха в виде медных шин, проложенных по стене. Сечение шинопровода рассчитывается из того, чтобы у отдаленного потребителя напряжение источника не снизилось более чем на 5%.
Постовые баластные реостаты R1, R2 нужны для выполнения функции развязки, регулирования режима и формирования пада-ющей характеристики. Вторая система питания (рис. 7.24, б) обеспечивает раздельное и глубокое регулирование тока и напря-жения. Постовое устройство представляет собой тиристорный выпрямительный блок, с помощью которого формируется характеристика любого типа, что придает источнику универсальность.
а б
Рис. 7.24. Схемы многопостовых выпрямительных систем:
а – с постовыми регуляторами, б – с постовыми выпрямительными блоками
Сварочные генераторы преобразуют механическую энергию якоря в электрическую энергию постоянного тока, необходимую для сварки. Различают коллекторные и вентильные генераторы. Коллекторные генераторы классифицируют в зависимости от способа возбуждения и получения необходимых внешних характеристик. В настоящее время в России коллекторные генераторы с независимым возбуждением и последовательной размагничивающей обмоткой, с самовозбуждением и последовательной размагничивающей обмоткой заменены на вентильные генераторы. Вентильные генераторы представляют собой комбинацию генератора переменного тока и выпрямительного блока. Переменный ток может вырабатываться синхронным индукторным генератором, синхронным с ротором явнополюсной конструкции и реже асинхронным генератором.
Синхронный генератор с ротором явнополюсной конструкции легче индукторного, но менее надежен из-за наличия скользящего токоподвода, асинхронный самый легкий, но труден в регулировании режима. В России используется индукторный генератор повышенной частоты (150…400 Гц). В зависимости от требуемой технологии в различных видах электросварки нашли применение разные виды источников питания.
Контактную электросварку осуществляют переменным или постоянным током. При ИП постоянного тока сварочная нагрузка распределяется по трем фазам питающей сети равномерно, но график ее остается неравномерным. Коэффициент мощности таких установок при номинальной нагрузке составляет 0,7…0,8; на холостом ходу он снижается до 0,4.
Электросварочные установки переменного тока имеют однофазную нагрузку в виде сварочных трансформаторов для дуговой сварки и сварочных аппаратов контактной сварки. Сварка на переменном токе представляет собой однофазную нагрузку с неравномерной загрузкой фаз и низким (0,3…0,35 для дуговой и 0,4…0,7 для контактной сварки).
К специальным видам сварочных установок относят: высокочастотные, плазменные, электрошлаковые, лазерные, электронно-лучевые. Широкое распространение получили высокочастотные сварочные установки: в производстве сварных труб, оболочек электрических кабелей, при изготовлении различных профилей. Этот вид сварки обладает меньшей энергоемкостью, чем дуговая и контактная сварки, и не имеет ограничений по скорости выполнения работ. Высокочастотная сварка труб осуществляется на трубоэлектросварочных станах (ТЭС) с использованием различного электрооборудования с установленной мощностью до 50 МВт, напряжение питающей сети 6, 10 кВ.
В настоящее время в энергомашиностроении, авиационной, судостроительной и других отраслях промышленности изготовление сварных конструкций затруднено, а в ряде случаев невозможно без применения электронно-лучевой сварки (ЭЛС). Такими примерами могут служить технологические процессы изготовления диафрагм паровых турбин, роторов электрических машин и др. Благодаря использованию электронного пучка с малыми ( ) углами сходимости, а также применению двойного преломления пучка можно получить сварные соединения с отношением глубины проплавления к ширине шва до 20:1.
Вакуум при ЭЛС обеспечивает получение металла шва с минимальным содержанием вредных примесей при сварке высокоактивных материалов. По сравнению с традиционными способами ЭЛС позволяет повысить скорость сварки в 10…15 раз, снизить расход конструкционных материалов на 10…15%, а сварочных – на 60…100%, уменьшить потребление электроэнергии на 30…80%, существенно улучшить условия труда сварщиков. Но оборудование для ЭЛС имеет высокую стоимость и сложность по сравнению с оборудованием для других способов сварки.
В качестве источников питания для ЭЛС могут быть применены высоковольтные ИП постоянного тока, состоящие из повышающих трансформаторов и высоковольтных выпрямителей, собираемых на тиратронах или селеновых элементах, а также на кремниевых диодах. На крупных установках для стабилизации тока пучка применяются параметрические источники тока [25]. Разработаны новые инверторные источники для питания прямоканальных ЭЛС мощностью до 4 кВт (табл. 7.12). Высоковольтный источник питания состоит из инвертора и выпрямителя.
Отличительной особенностью источника является то, что время отключения высокого напряжения в условиях межэлектродных пробоев в электронной пушке составляет порядка 0,3 мс, что повышает стабильность формирования сварных соединений.
Таблица 7.12
Техническая характеристика высоковольтного комплекса
Параметр | Значение |
Ускоряющее напряжение плавно регулируемое, кВ | 7…60 |
Ток сварки, мА | |
Ток накала катода, А | 5…60 |
Управляющее напряжение на прикатодном электроде плавно регулируемое, В | 0…5000 |
Питание от сети переменного тока: напряжение, В частота, Гц потребляемая мощность, кВ·А, не более |
220 ![]() |
КПД | 85…90% |
Габариты, мм высоковольтный выпрямитель блоки инверторов |
1300 ![]() ![]() ![]() ![]() |
Масса аппаратуры, кг, не более |
Рис. 7.25. Схема сварки неплавящимся электродом в инертных газах: 1 – мундштук, 2 – электрод, 3 – сопло, 4 – присадочный пруток, 5 – изделие, 6 – защитный газ |
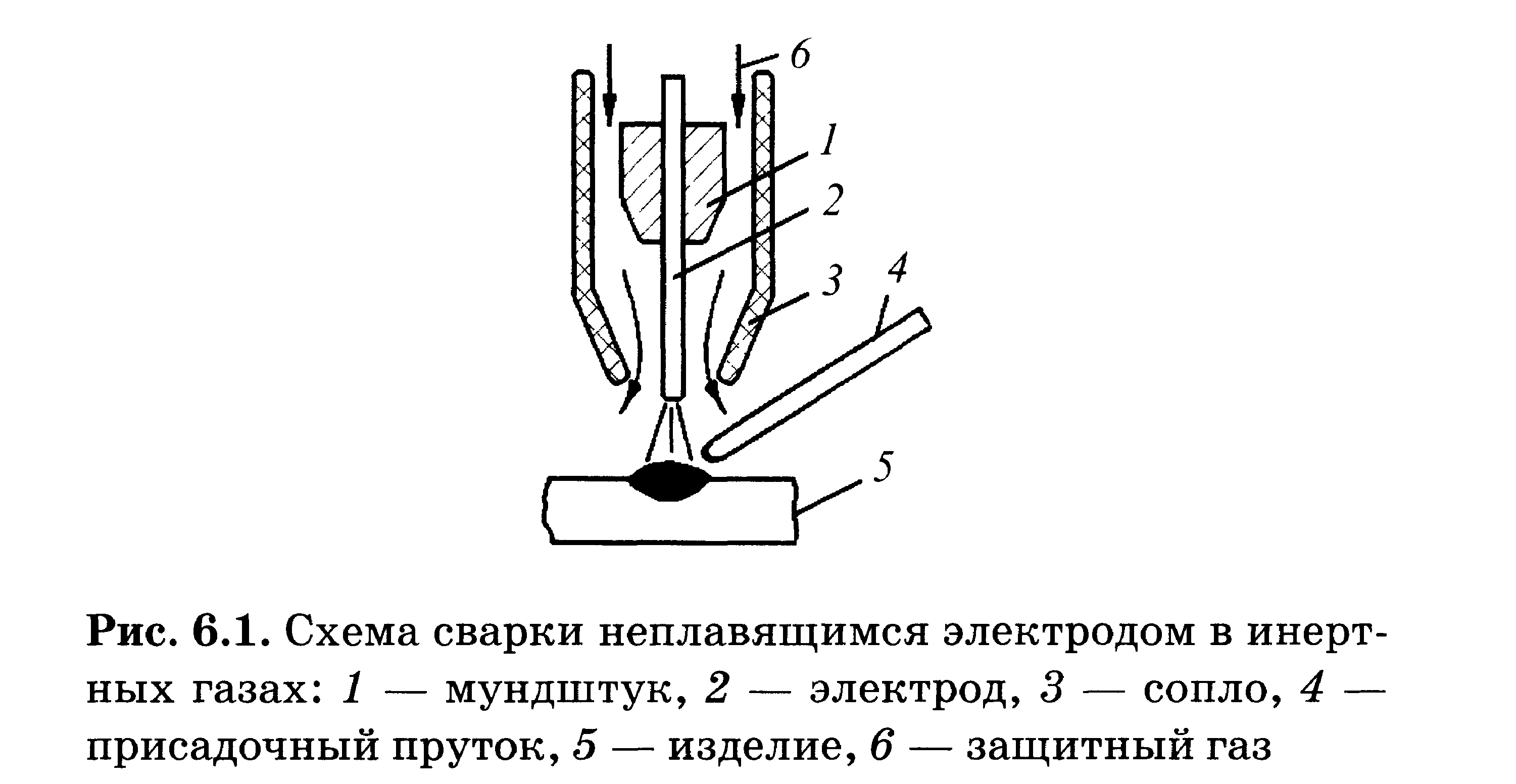
Требования к источнику питания определяются родом сварочного тока (постоянный, переменный) и характером его модуляции (непрерывный, импульсный, униполярный, импульсный разнополярный, высокочастотный), которые зависят от марки и толщины свариваемого металла. Источник постоянного тока (рис. 7.26) используется для сварки материалов средней и малой толщины за исключением алюминиевых сплавов. Сварка выполняется дугой прямой полярности (минус на вольфрамовом электроде). В сравнении с дугой обратной полярности здесь более благоприятное распределение тепла дуги, так как большая часть тепла идет на анод – изделие, что позволяет увеличить токовую нагрузку на электрод и тем самым поднять производительность. Однако дуга обратной полярности обладает важным технологическим свойством: при ее действии с поверхности свариваемого металла удаляются оксиды и загрязнения. Источник представляет собой трансформатор и выпрямительный блок на диодах или на тиристорах (типа ВД-306УЗ, ВД-306Э). Для формирования падающей внешней характеристики и плавного регулирования сварочного тока используется управляемый реактор, включенный во вторичную цепь трансформатора. Пост аргоно-дуговой сварки на постоянном токе можно собрать по схеме (рис. 7.26) на основе ИП общепромышленного назначения. Для таких целей могут использоваться выпрямители для ручной сварки с крутопадающей характеристикой серии ВД или тиристорные выпрямители серии ВДУ.
Рис. 7.26. Блок-схема источника постоянного тока
Источники питания серии ВДУ, называемые универсальными сварочными выпрямителями, предусматривают переключение для работы как с жесткими, так и с падающими внешними характеристиками. Они обеспечивают плавное дистанционное регулирование выходных тока и напряжения, стабилизацию режима при изменении напряжения сети. Кроме того, нужны осциллятор или возбудитель, дополненные фильтром высокой частоты, горелка и газовая аппаратура. В общий комплект источника питания часто включается также секционированный дроссель, обеспечивающий необходимые динамические характеристики для нормального переноса электродного металла в шов.
Возможно использование транзисторного выпрямителя или инверторного источника ВД-306Ф. Технические характеристики выпрямителя ВД-306Э (трансформаторного источника) и инверторного ВД-306Ф представлены в табл.7.13 [28].
Таблица 7.13
Сравнительные технические характеристики
Параметр | ВД-306Э | ВД-306Ф |
Максимальный ток, А | ||
Максимальная мощность, кВт | 9,77 | |
КПД,% не менее | ||
Потребляемая мощность, кВА |
Такие источники могут использоваться и для сварки пульсирующей дугой. Защита источника от высокого напряжения осциллятора производится с помощью фильтра высоких частот. Мягкий (холодный) пуск осуществляется при токе короткого замыкания, в несколько раз меньше сварочного тока, поскольку при обычном коротком замыкании наблюдается загрязнение шва вольфрамом и повышенный расход электрода. В сравнении с высокочастотным при мягком пуске ниже уровень электромагнитных помех, наводимых источником в сети.
Необходимая по технологии заварка кратера обеспечивается посредством плавного снижения тока с помощью специального устройства. Регулятор тока воздействует на тиристорный выпрямительный блок или обмотку управления трансформатора. В современных конструкциях настройка тока выполняется с помощью инвертора или полупроводникового регулятора.
Требования к источнику для сварки на постоянном токе распространяются и на большинство других источников для сварки неплавящимся электродом. Характеристика условной рабочей нагрузки соответствует уравнению , т.е. рабочее напряжение почти в 1,5…3 раза ниже, чем при сварке покрытым электродом. Внешняя характеристика должна быть падающей с напряжением холостого хода 50…100 В, т.е. в 4…6 раз превышающем рабочее, тем самым обеспечивается устойчивость процесса сварки и стабильность тока при колебаниях длины дуги, являющейся важной при малой толщине изделия. Регулирование тока должно быть плавным с очень высокой кратностью (не менее 5, иногда и до 100). Это необходимо, в частности, для снижения тока при заварке кратера или мягком пуске.
Программное управление последовательностью и длительностью включения отдельных устройств сварочной установки иллюстрируется на циклограмме (рис. 7.27) [26, 27]. Газ до сварки подается в интервале для надежного обеспечения возбуждения дуги и качественной защиты шва. Зажигание дуги выполняется высокочастотным разрядом в течение не более 1 с или мягким пуском. Сила тока мягкого пуска
назначается на уровне 0,1…0,3 от сварочного. Длительность мягкого пуска
обычно не настраивается, она ограничена либо прекращением контакта электрода с деталью, либо опусканием кнопки на горелке. Плавное нарастание основного тока (
) обеспечивает постепенный нагрев электрода. Тем самым предотвращается начальный выплеск сварочной ванны.
Рис. 7.27. Циклограмма аргоно-дуговой сварки
Снижение тока в течение необходимо для заварки кратера, увеличивающееся по продолжительности при большой толщине изделия и высоком значении сварочного тока. Подача газа после сварки необходима для защиты шва в процессе кристаллизации и остывания, это время
зависит от размеров сварочной ванны.
Управление циклом при аргоно-дуговой сварке с помощью кнопки на горелке может выполняться в вариантах с двух- и четырехкратным циклом. При двухтактном цикле после нажатия кнопки последовательно проходят этапы предварительной подачи газа, зажигания, нарастания тока и собственно сварки, для завершения цикла кнопку отпускают, в результате установка переходит к этапам снижения тока и подачи газа после сварки. Такой цикл предпочтителен для получения коротких швов. Четырехтактный цикл – после нажатия на кнопку следует подача газа до сварки, зажигание и работа в режиме поисковой дуги (мягкий пуск, пока нажата кнопка). После отпускания кнопки следует нарастание тока и длительная сварка до следующего нажатия кнопки. При втором нажатии осуществляется снижение тока для заварки кратера, а при отпускании кнопки отсчитывается время подачи газа после сварки.
Использование для сварки неплавящимся электродом переменного тока в определенной степени позволяет сочетать преимущества дуги постоянного тока прямой и обратной полярности. Однако асимметрия электрических свойств дуги при обратной полярности, обусловленная ее меньшей электрической проводимостью по сравнению с прямой полярностью, приводит к ряду нежелательных сопутствующих явлений. В результате выпрямляющей способности дуги появляется постоянная составляющая тока прямой полярности. В этих условиях дуга горит неустойчиво, ухудшается очистка поверхности сварочной ванны от тугоплавких оксидов и нарушается процесс формирования шва. Технологически оптимальный диапазон асимметрии должен находиться в интервале 02,..0,4, поскольку ниже этого значения не гарантируется достаточное качество очистки, а выше – заметно снижается стойкость вольфрамового электрода.
Для питания дуги в аргоне переменным током применяют специальные источники тока. В их схему включается стабилизатор горения дуги – электронное устройство, подающее импульс дополнительного напряжения на дугу в полупериод ее горения на обратной полярности. Так обеспечивается устойчивость дуги, постоянство тока и процесса формирования шва на обеих полярностях. Высокочастотные источники для аргоно-дуговой сварки обычно создаются на базе инверторного (рис. 7.28). Переменный высокочастотный ток получается путем попеременного включения вентилей VT1 и VT2. На дугу подаваться может как переменный ток от трансформатора Т (рис. 7.28, б), так и от несглаженного выпрямленного с блока V2, при необходимости с двойным модулированием (рис. 7.28, в и г).
а б
в г
Рис. 7.28. Инверторный импульсный источник:
а – упрощенная схема, б – импульсный переменный ток,
в – амплитудное, г – частотное моделирование постоянного тока
Пульсирующий ток может быть получен и из постоянного с помощью высокочастотного полупроводникого преобразователя. Получили распространение универсальные по роду тока источники питания. Один источник можно использовать для сварки, например, алюминиевых сплавов на переменном токе, для остальных металлов – на постоянном.
Установка для аргонодуговой сварки неплавящимся электродом УДГУ-302 имеет в своем составе автоматический выключатель, QF, контактор K1, силовой трансформатор T1 с увеличенным рассеянием, вентильный блок VD1, VS2-VS6, универсальный блок подпитки VD2, VD3, R1, R2, VS7, блок подпитки постоянного тока Т2, VD4, R3, конденсатор высокочастотный фильтра С1 и блок поджига дуги А (рис. 7.29).
а
б в
Рис. 7.29. Принципиальная схема (а), осциллограммы переменного (б)
и постоянного (в) тока установки УДГУ-302
Необходимым оборудованием для аргоно-дуговой сварки является горелка. Горелка (рис. 7.30) осуществляет закрепление электрода, подачу защитного газа и подвод сварочного тока и воды. Каждая сварочная горелка комплектуется запасными и сменными соплами и цангами соответствующих диаметров. Для смены цанги 2 следует отвернуть тыльный колпачок 4 и вынуть цангу со стороны сопла, а на ее место установить цангу соответствующего диаметра. Вольфрамовый электрод вставляется со стороны сопла и затягивается в цанге с помощью тыльного колпачка.
Рис. 7.30. Горелка малая ГР-4:
1 – сопло; 2 – цанга; 3 – корпус; 4 – тыльный колпачок; 5 – выключатель;
6 – рукоятка; 7 – токоподвод; 8, 9 – трубки соответственно для подвода газа
и подвода воды; 10 – подвод к выключателю
НПП «Технотрон» производит полную гамму промышленного сварочного оборудования высочайшего качества. Современным промышленным аппаратом для сварки неплавящимся электродом в защитных газах сталей и цветных металлов, в том числе алюминия и его сплавов на постоянном и переменном токе до 315 А, является аппарат ДС315АУ.33. Имеет режим работы для сварки покрытым электродом (РДС, ММА) на токах до 250 А. Аппарат может эксплуатироваться при питании как от стационарной сети, так и от автономных источников.
Для сварки алюминия и его сплавов предусмотрен режим работы на переменном токе с регулировкой амплитуды, частоты и коэффициента заполнения импульсов сварочного тока, т.е. обладает возможностью увеличения либо уменьшения доли сварочного тока прямой и обратной полярности. Это позволяет гибко управлять проплавляющей и очищающей способностью сварочной дуги. Повысить проплавляющую способность дуги можно, увеличив до-лю сварочного тока прямой полярности или его амплитуду. Повысить очищающую способность сварочной дуги, необходимую для эффективного разрушения оксидной пленки, можно, увеличив сварочную долю тока обратной полярности или его амплитуду. Такое управление тепловложением позволяет значительно увеличить стойкость электрода и использовать горелку без водяного охлаждения. Технические характеристики представлены в табл. 7.14 [12].
Таблица 7.14
Основные технические данные аппарата ДС315АУ.33
Параметр аппарата | Значение характеристик |
Потребляемая мощность, кВ∙А, не более | |
Напряжение питания, В | 380, +10%-15% |
Сварочный ток (дискретность регулировки 1А), А: в режиме АДС в режиме РДС | 10-315 10-250 |
Частота переменного сварочного тока в режиме АДС, Гц (дискретность регулировки 1 Гц) | 30-200 |
Отношение длительности импульсов прямой и обратной полярности в режиме АДС, % | 30-70 |
Способ возбуждения дуги в режиме РДС | Контактный и бесконтактный |
Режим работы | Непрерывный и импульсный |
Частота модуляции в аргоно-дуговом режиме, Гц | 300 ![]() |
Номинальный режим работы ПН, % (при + 20ºС) | |
Диапазон рабочих температур, ºС в режиме АДС в режиме РДС | От – 10 до + 40 От – 40 до + 40 |
Габаритные размеры, мм | 564 ![]() ![]() |
Рис. 7.31. Общий вид аппарата для полуавтоматической сварки ДС200К.3 |

Установка продольной сварки ТТ198 предназначена для автоматической сварки продольных швов цилиндрических деталей в цеховых условиях, снабжена системой автоматического поддержания длины дуги. Источник инверторного типа может работать в непрерывном и импульсном режимах.
В источниках всех перечисленных аппаратов предусмотрено автоматическое отключение при перегреве, отсутствии одной из фаз или снижении питающего напряжения более, чем на 15% Характеристики источников не зависят от колебаний напряжения питающей сети.
Контактная сварка – термомеханический процесс образования неразъемного соединения металлов, при котором локальный нагрев свариваемых деталей, протекающим электрическим током, сопровождается пластической деформацией под действием сжимающего усилия.
Сварочные установки для контактной сварки имеют две основные части: электрическую и механическую. Электрическая часть состоит из сварочного трансформатора специальной конструкции, токопроводов и устройств для включения и выключения сварочного тока. Механическая часть установок представляет собой устройство для импульсного сжатия свариваемых деталей.
Машина для точечной контактной сварки марки BN10C чехословацкого производства, технические характеристики которой представлены в табл. 7.15, предназначена для сварки листов из малоуглеродистой стали толщиной до 6 мм для ремонтов в условиях мелкосерийного производства.
Таблица 7.15
Основные технические данные машины BN10С
Параметр машины | Минимальное значение | Максимальное значение |
Потребляемая мощность, кВ∙А | ||
Первичное напряжение, В | ||
Первичный ток, А | 26,3 | 65,8 |
Коэффициент нагрузки, % | ||
Вторичное напряжение, В | 1,4 | 2,8 |
Окончание табл. 7.15 | ||
Параметр машины | Минимальное значение | Максимальное значение |
Вторичный ток, А | 2,500 | |
Число ступеней переключателя | ||
Длина хода электродов, мм | ||
Вылет электродов, мм | ||
Сила нажатия между электродами при вылете 400 мм, кН | 1,3 (δ = 2 мм) | 3 ,3 (δ = 6 мм) |
Сила нажатия между электродами при вылете 250 мм, кН | 3,0 (δ = 2 мм) | 5,0(δ = 5 мм) |
Расход охлаждающей воды, л/ч |
Особенностью цикла контактной сварки является кратковременность работы составляющих его элементов. Надежность сварочных соединений зависит от правильности выбранного режима сварки, его стабильной повторяемости. Это определяет требования к аппаратуре управления, которая должна быть максимально автоматизирована, малоинерционна, обладать чувствительностью, точностью работы и эксплуатационной надежностью.
При помощи аппаратуры управления осуществляется включение, регулирование и выключение сварочного тока, регулирование последовательности и продолжительности отдельных операций цикла сварки, в том числе времени протекания тока, изменения частоты вращения роликов шовной машины или перемещения подвижной плиты стыковой машины, включение и регулирование условий сжатия электродов и т.п. В контактных машинах сварки чаще используется аппаратура управления однофазными машинами. Это регуляторы времени, прерыватели, вентильные контакторы. Регуляторы цикла сварки регулируют ток и стабилизируют его при колебаниях напряжения сети. Как правило, однофазные машины переменного тока оснащены тиристорными контакторами, различающимися коммутируемым током.
Усложнение технологических циклов сварки, постоянное усовершенствование машин контактной (точечной, шовной, стыковой) сварки, рост потребности в тончайших настройках регуляторов контактной сварки заострило необходимость производить микропроцессорные регуляторы контактной сварки (например, типа РКС). В настоящее время находят применение новые серии РКС 602 и РКС 802. При контактной сварке основными источниками радиопомех являются исполнительные механизмы (электроды, ролики), электроаппаратура управления процессами сварки (реле, контакторы, тиристорные прерыватели, электронные регуляторы времени и др).
Рис. 7.32. Машина шовной сварки |
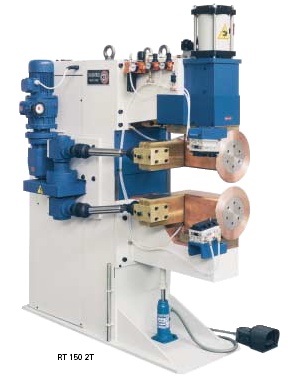
Важным вопросом при рассмотрении сварочного оборудования является влияние сварочных агрегатов на качество электрической энергии. Основными видами помех, создаваемых сварочным оборудованием, являются отклонения, колебания и провалы напряжения, несинусоидальность тока и напряжения, несимметрия напряжения.
Таблица 7.16
Технические характеристики машины контактной сварки
Технический параметр | Модель | |||||
RT80 | RT81 | RL81 | RTL81 | RT100 | RT1502Т | |
Привод: C – зубчатый ремень, D – кардан, Е – дифференциал | С | D | D | D | D | E |
Напряжение питания при 50 Гц, В | ||||||
Номинальная мощность при 50% ПВ, кВ·А | ||||||
Напряжение вторичной обмотки, В | 5,1 | 6,7 | 6,7 | 6,7 | 7,9 | 9,5 |
Вылет электродов, мм | ||||||
Окончание табл. 7.16 | ||||||
Технический параметр | Модель | |||||
RT80 | RT81 | RL81 | RTL81 | RT100 | RT1502Т | |
Полезный вылет, мм | ||||||
Рабочий ход , мм | ||||||
Скорость сварки, м /мин | 0,6-4,2 | 0,6 | 4,2 | 0,6 | 0,8-5,0 | 0,8-5,0 |
Диапазон сварки по листу из низкоуглеродистой стали, мм | 1,2+1,2 | 1,2+1,2 | 1,2+1,2 | 1,2+1,2 | 1,5 | 2+2 |
Диапазон сварки по листу из нерж. стали, мм | 1,5+1,5 | 1,5+1,5 | 1,5+1,5 | 1,5+1,5 | 2+2 | 3+3 |
Усилие (при 6 атм. в системе), кН | 4,7 | 4,7 | 4,7 | 4,7 | 9,0 | 12,0 |
Габариты, мм | ||||||
Вес, кг |
Импульсный характер графиков нагрузки электросварочных машин приводит к появлению в огибающей кривой напряжения провалов напряжения. Форма провала напряжения зависит от типов сварочных машин и режимов их работы. Глубина провалов определяется мощностью сварочной машины и мощностью источников питания. Машины точечной и рельефной сварки создают провалы напряжения до 7%.
В настоящее время все большее число сварочных машин снабжается регулируемыми тиристорными контакторами. Большое распространение получили также сварочные машины постоянного тока и установки дуговой сварки постоянного тока для плавного регулирования действующего значения сварочного тока (игнитронные и тиристорные контакторы применяются с регулируемым углом зажигания игнитронов или регулируемым углом открытия тиристоров).
Сварочные машины в основном являются однофазными потребителями электроэнергии [17]. Равномерно распределять их по парам фаз трехфазной сети не всегда удается, особенно крупные сварочные машины; кроме того, сварочные машины включаются в работу в случайном порядке. Поэтому в трехфазной сети со сварочными машинами возникает несимметрия токов, которая приводит к несимметрии напряжений. Наряду с системой прямой последовательности напряжений появляются составляющие обратной и нулевой последовательности. Характер и числовое значение несимметрии в цеховой сети низкого напряжения зависят от схемы соединений обмоток цеховых трансформаторов, от типа сети низкого напряжения и параметров ее элементов. Цеховые трансформаторы в настоящее время выпускаются со схемой соединения обмоток У/У0 и Д/У0. Все сварочные машины включаются на линейное напряжение. При отсутствии электроприемников, включенных на фазное напряжение, несимметрия токов и напряжений будет обусловлена лишь наличием составляющих обратной последовательности.
Несимметрия напряжения, вызываемая сварочной нагрузкой, может сказаться на схемах управления и автоматики сварочных машин и других производственных механизмов. Системы управления современных сварочных установок, линий и цехов сегодня часто автоматизированы и состоят из электронных узлов и элементов. Возможны влияния как опасные, так и мешающие. Перенапряжения в питающей сети, а также даже самые кратковременные скачки напряжения могут привести к пробою изоляции или выходу из строя элементов электронной, особенно полупроводниковой, техники и тем самым вывести из строя ЭВМ (либо другое электронное устройство), подчас в наиболее ответственный момент, когда требуется особенно четкая и бесперебойная работа. Близко расположенные и недостаточно экранированные мощные электрические цепи, какими являются сети со сварочным оборудованием, могут создавать такие электромагнитные наводки в цепях питания и внутренних цепях электронных устройств, которые существенно затрудняют их работу.
Многие электронные устройства функционируют на частотах значительно выше промышленной частоты 50 Гц. Однако всевозможные высокочастотные электромагнитные колебания в цепях сварочных установок создают нежелательные помехи в указанных устройствах, работающих вблизи установок стыковой контактной сварки, сварочных линий и многоточечных контактных машин, являющихся весьма мощными электроэнергетическими приемниками. Повторные зажигания и погасания электрических дуг возникают при технологическом процессе сварки в установках дуговой сварки. Меньшей мощности дуги возникают в установках контактной сварки и различных коммутирующих аппаратах в цепях питания сварочных установок. Зажигания и погасания дуги возбуждают в коммутируемых контурах электромагнитные колебания, создающие помехи в расположенных вблизи от них электронных схемах (особенно актуально для приемников информации по радиоволнам).
Дата добавления: 2014-12-18; просмотров: 17081;